碳化硅模块提高电机驱动器的功率密度
Article
牵引驱动器是电动汽车(EV)几乎所有能量的消耗源。因此,驱动系统必须尽可能提高效率,同时以最低重量占用最小空间 — 这些均旨在尽可能提高电动汽车的续航能力。随着行业利用双驱动装置提高牵引力,同时借助 800 V 架构降低了损耗,该行业还需要尺寸缩小但输出功率增加的逆变器,实现远超硅(Si)基技术(如 IGBT)能力的功率密度。
Wolfspeed 的最新一代碳化硅(SiC)功率模块旨在凭借更低的损耗、更高的功率密度和更小的尺寸来满足以上需求。
本文介绍了 CRD600DA12E-XM3 三相双逆变器的参考设计,并揭示如何在下一代电动汽车牵引解决方案中结合相应组件(包括 CAB450M12XM3 功率模块和 CGD12HBXMP 栅极驱动器)及其他关键技术。
系统概述
CRD600DA12E-XM3 包含两组 CAB450M12XM3 功率模块,每组均带有 CGD12HBXMP 栅极驱动器(图 1)。总体设计目标是采用低成本、低复杂度的高载流量、低电感设计,最大限度提高性能。
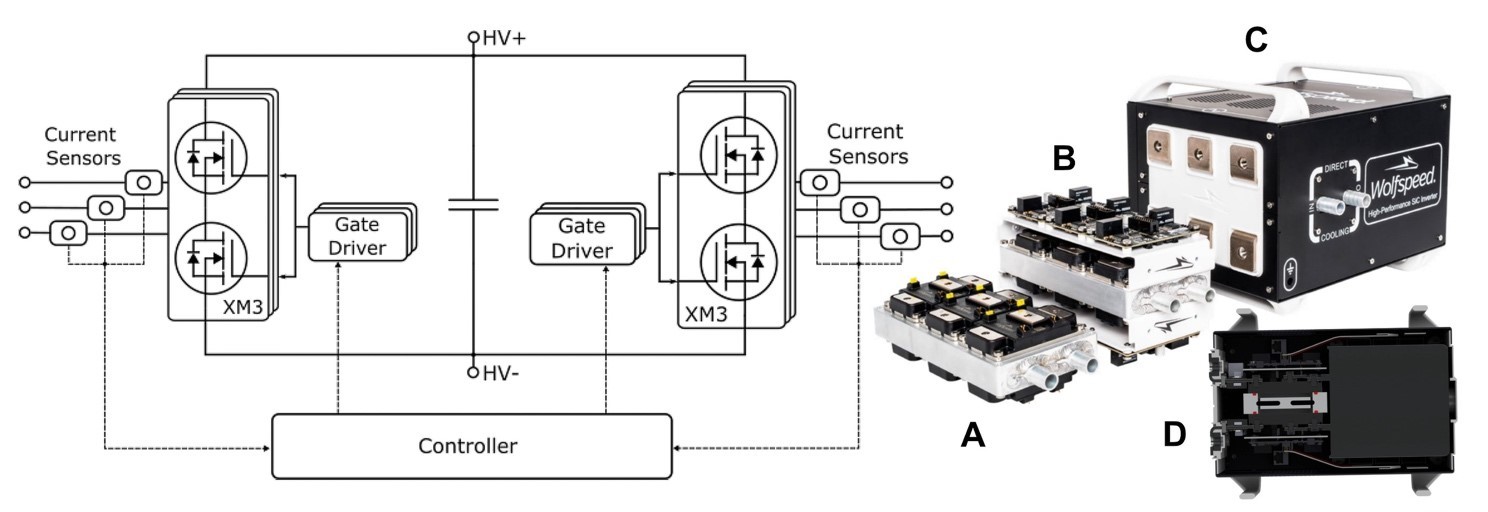
以及控制器。双逆变器外壳 (C) 的外部还显示有安装在冷板上以及带有栅极驱动器的电源核心 (B) 上的电源模块 (A)。提供手柄和底座,方便携带。D 显示横截面为 204 mm x 267.5 mm。
在设计系统时,需要考虑五个关键点:
- 使用碳化硅(SiC)技术可实现的高功率密度。虽然碳化硅(SiC)支持在更高温度下运行,但高功率密度需要采用先进的散热技术。
- 开关速度快会令系统更容易出现杂散电感引起的过冲和振铃;因此,需要降低母线结构的杂散电感。
- 针对这一问题,还需要采用低电感、高纹波额定电容,同时注意缩小尺寸。
- 栅极驱动器电路必须具备足够的驱动强度,以维持碳化硅(SiC)技术要求且支持的开关速度。
- 整体功率密度应明显较高,从而满足终端应用的要求。
首选功率模块平台:XM3
基于 Wolfspeed XM3 全碳化硅(SiC)平台的功率模块具有出色的功率密度,显然是不二之选。它的重量和体积大约是标准 62 mm 模块的一半,与 EconoDUAL 相比,差距更加显著(图 2)。
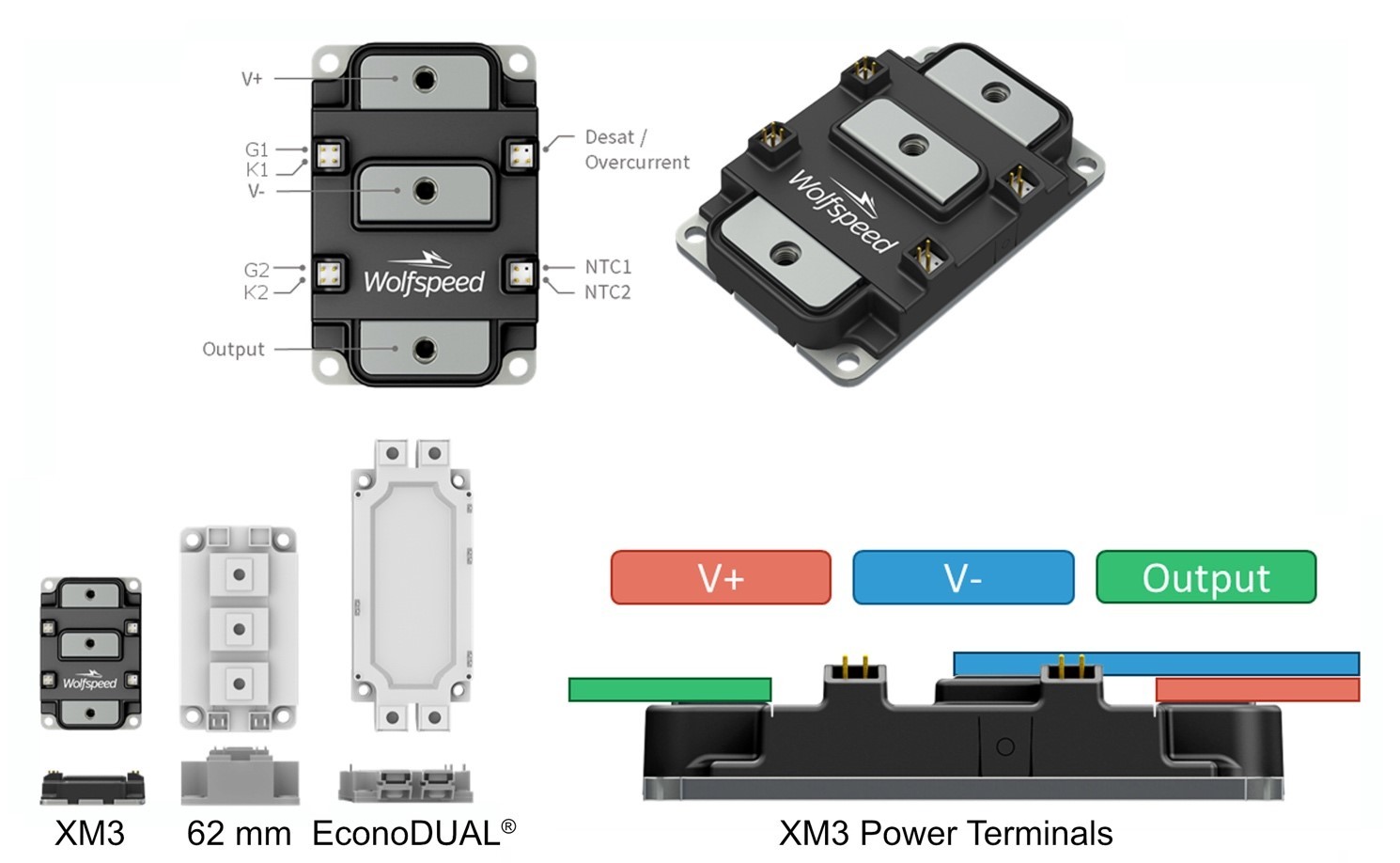
XM3 平台采用重叠的平面结构设计,以便实现低杂散电感。模块内的电流回路既宽且薄,在器件间均匀分布,从而在开关位置产生等效阻抗。模块的电源端子也能垂直偏移,使得直流链路电容和模块之间的简单母线设计能够一直层压到模块上。最终结果是,在 10 MHz 时,电源回路的杂散电感仅为 6.7 nH。
该模块的杂散电感仅为行业标准模块的一半,体积则不到一半,为 53 × 80 mm 规格。XM3 平台为不同的目标应用提供开关优化型和传导优化型产品,例如该系统使用的 CAB450M12XM3 1,200 V、450 A 半桥模块。
XM3 特性包括:低边开关位置的集成式温度传感器;便于驱动器集成的内置电压感应(de-sat)连接;以及增强功率循环能力的高可靠性氮化硅(Si3N4)电源基板。
逆变器系统的性能可通过以下几项技术得到进一步提升,从而提高散热效率,减少寄生电感,降低组件数量和尺寸。
冷板
碳化硅(SiC )器件支持的高电流密度需要高性能热叠层才能最大限度地提高热传导。在散热片的众多选择中,压制铜管是液冷板通用的经济化选项。虽然可以使用支持两侧模块安装的薄铜管冷板(约 12.7 mm),但两侧不同高热阻以及高压差的缺点也确实存在,会导致表面和两侧冷却的不一致性。
CRD600DA12E-XM3 在冷板中使用了 Wieland Microcool 的微变形技术(MDT)(图 3)。MDT 是一项低成本、非减材的专利制造工艺,可通过机械和塑性方式使工件变形,形成有限且可重复的微通道。
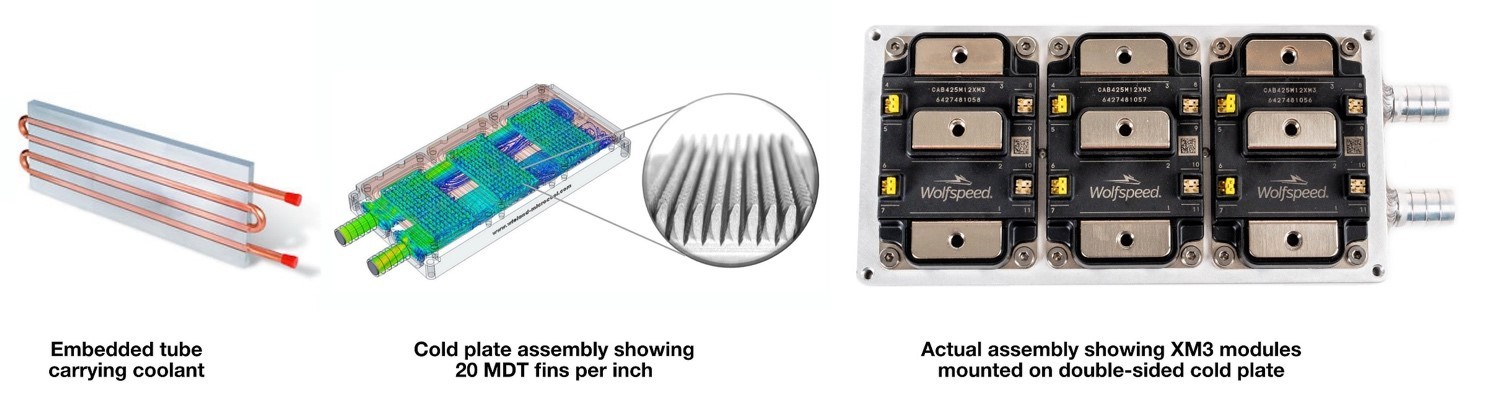
从而降低热阻,实现均匀冷却。
这是高性能冷板的基础,其具有的嵌入式通道可冷却 XM3 模块的整个接触面。双面 CP4012D-XP 冷板的外形经过优化,能够匹配 XM3 模块规格,尺寸较上一代 CP3012 有所缩小。
以 4 LPM 的速度为全部六个模块位置提供均衡的冷却液流量,形成 0.048℃/W(每个位置)或 0.008℃/W(每个冷板)的极低热阻。经测试,在使用 CAB450M12XM3 时,冷却系统每个开关的功耗可达 750 W。
驱动器强度
由于转换器模块的碳化硅(SiC)MOSFET 具有高功率性能,驱动器必须拥有足够大的驱动强度(峰值输出电流额定值或开关器件所用的电流值)才能维持较快的开关速度。建议采用 10 A 以上的额定值,确保较高边缘速率。Wolfspeed 的 CGD12HBXMP 栅极驱动器便可提供。
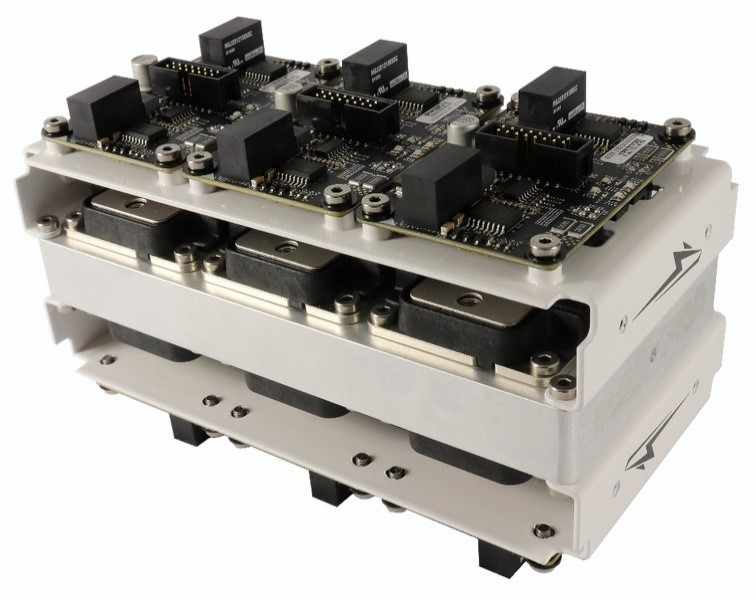
双通道栅极驱动器拥有过流和极性反接保护特性以及板载的 2 W 隔离型电源,能够支持 80 kHz 开关频率。用户可配置的开通和关断栅极电阻可减少开关损耗。
该驱动器还具备可调过流检测特性,拥有软关断、欠压锁闭以及 PWM 输入防重叠功能。它还提供约 2 µs 的启动到熄灭时间,以便在短路情况下安全关断。
由于碳化硅(SiC)MOSFET 具有较高的 dV/dt 速率,因此共模瞬态抗扰度(CMTI)额定值不足 会导致逻辑输出和驱动器输出之间的锁存,造成硬件故障。CGD12HBXMP 具有较高的 100 kV/μs CMTI 额定值、较低(<5 pF)的隔离电容和差分输入,能够提高抗噪能力。
CGD12HBXMP 还拥有与 XM3 模块相同的尺寸,能够将六个 CAB450M12XM3 模块及其驱动器集成在冷板上,形成紧凑的电源核心(图 4)。这项紧凑的解决方案能够轻松集成至双逆变器设计中。
直流链路电容
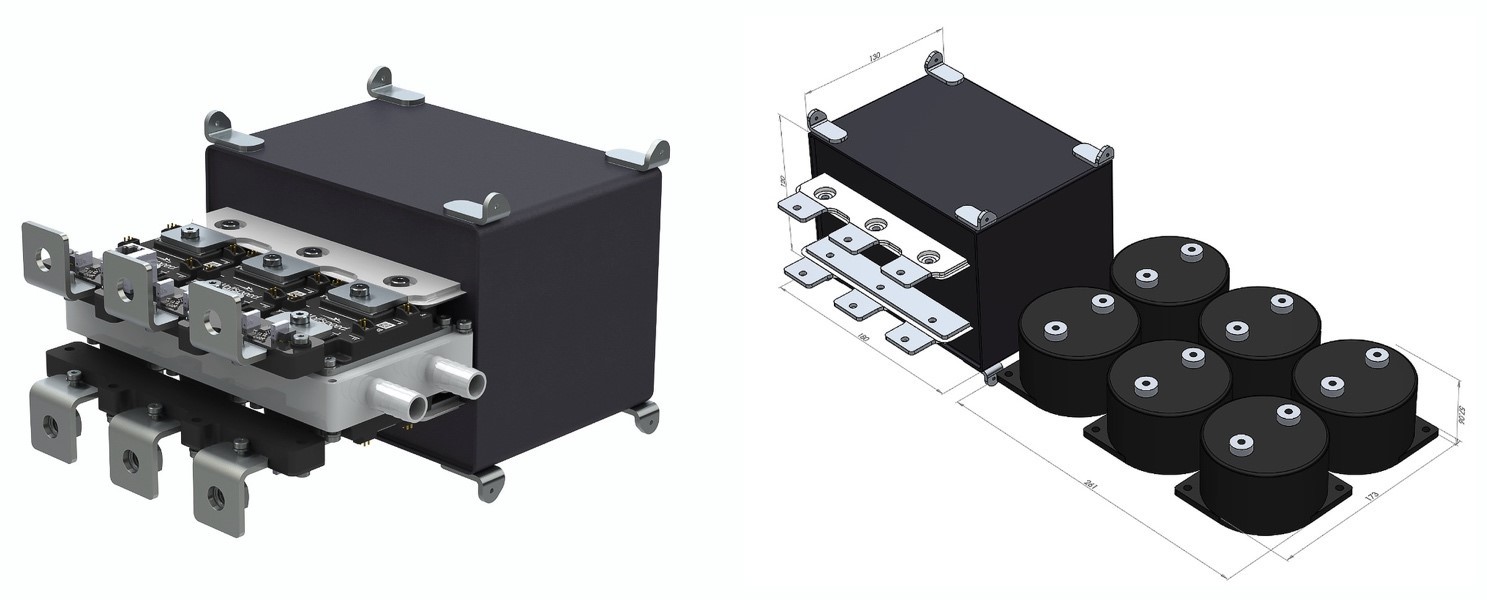
寄生电感的降低是一项关键问题,且如上所述,XM3 模块的垂直偏移电源端子部分降低了寄生电感,从而简化母线设计,降低电源回路电感。这一问题在图 5 所示的直流链路电容选择中得到了进一步解决。
电容规格是提高功率密度的最大障碍之一。通常会使用现成的六个 100 μF 圆柱形电容来达到所需的纹波电流额定值,规格为 451 cm2,并需要使用单独的母线。
Wolfspeed 使用了专门设计的直流链路电容(图 5),规格仅为 234 cm2。其特点是集成了叠层母线(连接至冷板两侧 XM3 电源模块的电源端子),降低了电源回路的寄生电感,确保两组模块实现均衡的电流路径。由于取消了单独的母线和硬件,组件数量也有所减少。 在电压为 900 V 时,定制电容为 600 µF,峰值电压额定值为 1,200 V。为了降低快速开关碳化硅(SiC)逆变器高 di/dt 速率下的常见电压尖峰,电容和集成母线杂散电感至关重要,在经阻抗分析仪测量端子处的 13 nH 等效串联电感后,该设计已得到验证。该电容结合 XM3 模块的 6.7 nH 电感,总电源回路电感仅为 20 nH,能够达到更快的开关速度。
控制器
在选择该系统的控制器板处理器时,需要考虑以下因素:
- 应当具备充足的处理“马力”,用于对所有输入进行采样,并作出控制决策。
- 应当具有足够多的 ADC 数量,能够测量所有必要的系统状态,进行适当的控制和监测。
- 应当具有快速硬件中断功能,用于响应故障情形。
- 必须支持标准通信,这对正常运行至关重要。
因此,该系统的控制器板使用了 Texas Instruments 的双核浮点 200 MHz 32 位 DSP。此 DSP 拥有充足的 ADC 输入来测量电流、电压和温度,并提供通信支持(包括隔离式 CAN)。
电流传感器
双逆变器在输出端子使用六个电流传感器。由于系统中的传感器数量较多,所选的传感器模块尺寸哪怕缩小一点,都会立即带来显著影响。虽然 COTS 电流传感器模块容易获得,但可能体积庞大。此外,市场上的一些三合一传感器模块加大了对母线几何形状的限制。
对于 CRD600DA12E-XM3 系统,Wolfspeed 选择了直流至 250 kHz Melexis MLX91208 霍尔效应传感器,能够提供与外部水平磁通密度成比例的高速模拟输出信号,响应时间低至 3 µs。
此传感器采用八引脚 SOIC 封装,体积小到可以安装在紧凑型 PCB 上,然后直接连接至输出母线。PCB 安装灵活,能够简化输出母线。
外,MLX91208 使用沉积在 CMOS 芯片上的集成式集磁片(IMC),从而无需较大的铁磁芯(图 6)。该组件规格为 91.6 mL,而汽车行业的另一通用传感器组件体积为 800 mL。
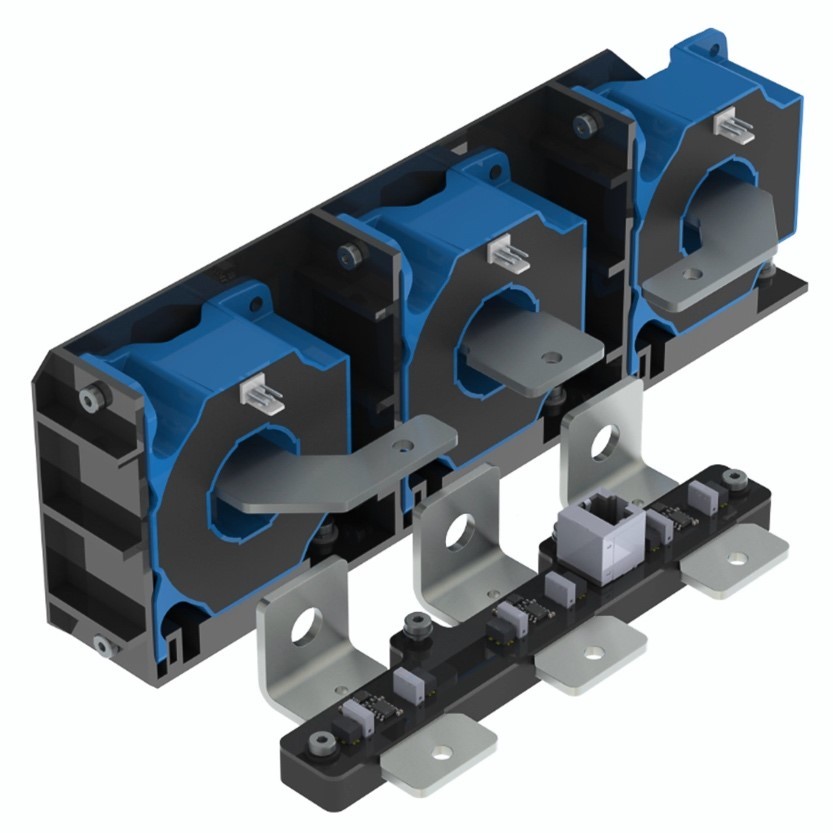
碳化硅(SiC)逆变器中典型的高 dV/dt 速率会令低压敏感信号(例如电流传感器的信号)产生噪声。电流传感器离开关节点很近,使之更易受到影响。传感器和控制器之间的电缆也是如此,系统周围的布线也会拾取到噪声。
Wolfspeed 选择的传感器只需叠层式 U 形磁屏,便可防止外场干扰,均匀磁场。PCB 的 接地层能够阻止母线到传感器的电容耦合。差分信号的使用显著降低了开关辐射噪声的影响。此外,在传感器板和控制器之间使用屏蔽双绞线 CAT6 电缆,可确保一对差分信号的噪声均为共模噪声。
测试性能
在苛刻的开关条件下使用低栅极电阻进行钳位电感负载双脉冲测试,验证整个电源回路。恒定电流负载波形显示,在 800 V 和 600 A 时,开通开关能量为 23.1 mJ,峰值电流过冲为 113 A。
关断开关能量为 30.1 mJ。芯片的母线电压裕量为 80 V,与模块的标称额定值相比,处于 2 倍过载状态。
接着,根据 300 A 标称条件下已知的 12.2 mJ 开通能量和 12 mJ 关断能量,计算每个模块的开关损耗。使用开关功率损耗(PSW)公式,
并插入 EON 和 10 kHz 的开关频率(fSW),
碳化硅(SiC)具有反向恢复能量(ERR)极低的巨大优势,这一损耗比同类 Si IGBT(HybridPack 1,200 V、380 A 标称值)低 3 倍。
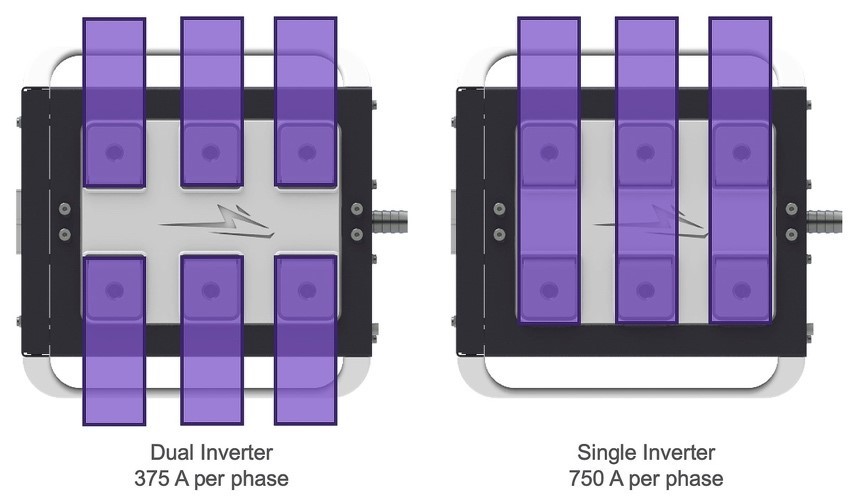
该设计还通过三相再循环负载测试在应用条件下进行了验证。
这一设计的输出端子排列灵活,简化了测试设置 — 六个输出端可用作两个独立的三相逆变器,每个逆变器为 375 ARMS,或者通过添加简单母线和并联相位,作为能够达到 750 ARMS 的单个三相逆变器(图 7)。
测试使用的是单逆变器设置,交流输出端 U 和 X 组合构成 A 相,V 和 Y 构成 B 相,W 和 Z 构成 C 相。三个 125 µH 负载电感连接在逆变器的某个输出端子和大型电容组的中点之间(每一半为 2.2 mF),额定电压为 1,100 V。
这样一来,便只需在几千瓦功率的情况下进行高功率测试,直流电压电源仅存在系统损耗。在每个开关周期内,能量通过电感器从一半电容转移至另一半,能量转移的方向会在一个基频周期中翻转。 在 800 V 的母线电压下经过五分钟测试,电容外壳温度比环境温度高 13℃,栅极驱动器热点的实测温度比环境温度高 40℃。对于 10 kHz 的开关频率和 300 Hz 的基频,RMS 并联输出电流为 750 A,相当于 624 kW 的输出功率。在 10 kHz 时,所选负载电感的电流纹波为 160 A,峰值组合电流达到 1,200 A(包括电流纹波)。
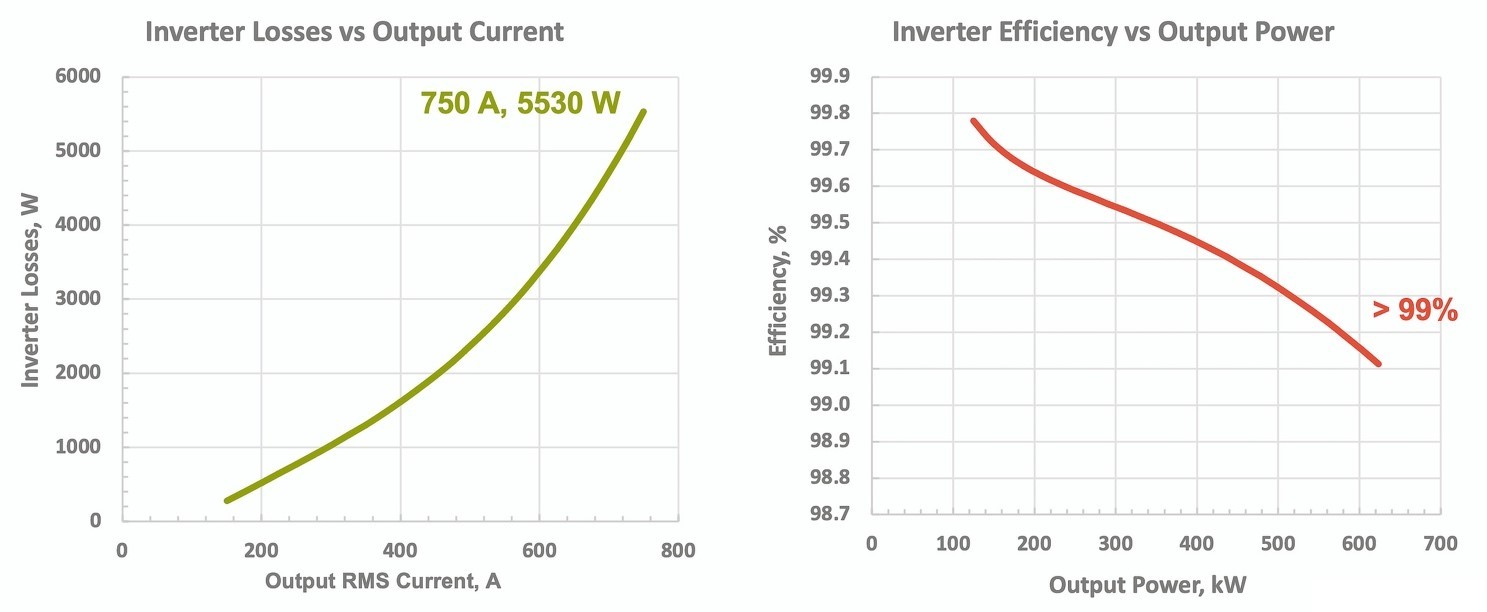
10 kHz、375 A 时的开关能量为 31 mJ。关于每个开关 5.53 kW 或 460 W 的总损耗,开关损耗为 1.8 kW。因此,最高达 624 kW 的逆变器效率超过 99%(图 8)。
总结
CRD600DA12E-XM3 三相双逆变器参考设计满足上述五项关键设计因素,利用 CAB450M12XM3 电源模块实现 624 kW 的峰值输出功率和每相 375 Arms 或并联 750 Arms 的额定电流。
Competitor | CRD300DA12E-XM3 | CRD600DA12E-XM3 | |
Semiconductor | Si IGBT | SiC | SiC |
Type | Single Inverter | Single Inverter | Single Inverter |
Output Power | 250 kW | 300 kW | 624 kW |
Volume | 12.6 L | 9.3 L | 8.6 L |
Power Density | 19.8 kW/L | 32.2 kW/L | 72.5 kW/L |
这一解决方案采用 204 × 267.5 × 157.5 mm 的全金属外壳(如图 1 所示),重 9.7 kg,体积仅为 8.6 L,即可达到 72.5 kW/L 的超高功率密度,比此前的 300 kW 碳化硅(SiC)参考设计高出一倍以上,比等效额定 IGBT 逆变器的潜在值高 3.6 倍(表 1)。
如需了解有关 CRD600DA12E-XM3 三相双逆变器参考设计、CAB450M12XM3 功率模块和 CGD12HBXMP 栅极驱动器的更多信息,请联系 Wolfspeed 功率应用团队。