Add Miles and Years of Performance to Your Next 800-V EV Traction Inverter Platform


Article
In order to achieve a zero emissions future, the automotive industry must reinvent itself. The evolution of internal combustion engine (ICE) vehicles took decades to become what we know and drive today. New electric vehicles are expected to offer the same comforts, driving experience, longevity and safety as their ICE predecessors. With this, automakers must bring to the market new differentiated electric models with equal or superior performance and do it fast. It requires making bold decisions, trying new material, and finding partners with the same vision and hunger for innovation.
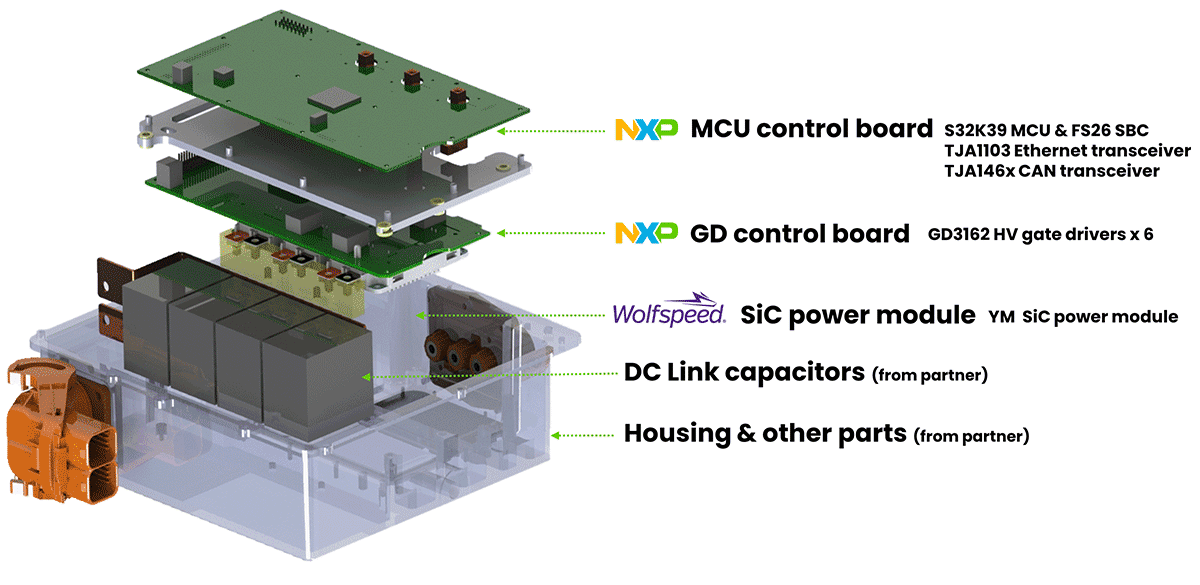
To support their automotive partners and facilitate the race to vehicle electrification, NXP and Wolfspeed joined together delivering a fully tested 800 V Traction Inverter Reference Design that mitigates many of the hurdles facing an EV system architect, including component selection to increase the system efficiency, meeting functional safety certification standards and ensuring life-long reliability.
The EV Traction Inverter Reference Design is a full-system solution containing Arm® Cortex®-M7 based S32K39 MCU with functional safety compliant power management FS26 system basis chip and the latest generation of high voltage isolated gate drivers GD3162. To complete the system the 1200 V six-pack YM SiC power modules from Wolfspeed has been associated.
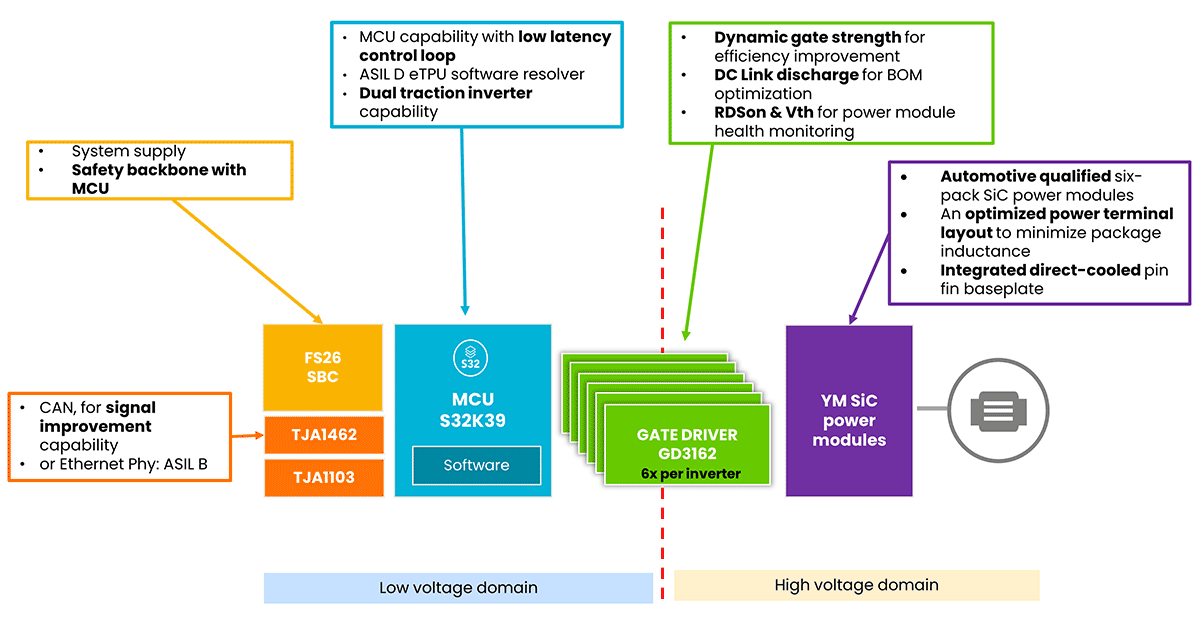
This EV traction inverter reference design has been tested jointly with Hardware in the loop (HIL) setup at Wolfspeed Munich Laboratory. Under an 800-volt battery condition a performance of over 300 kilowatts at peak power has been reached.
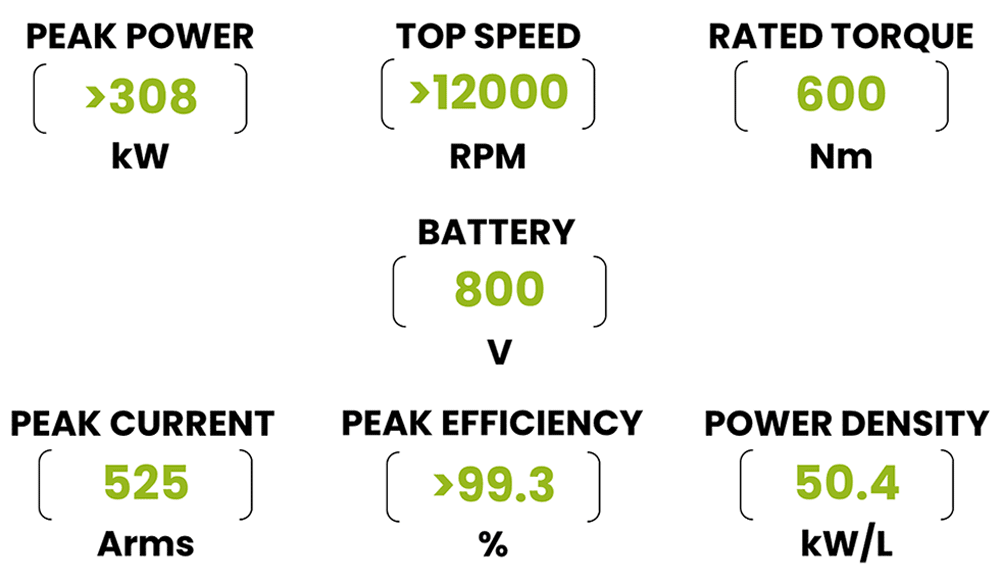
Design for Maximum Efficiency: Dynamic Gate Strength Adapting to Varying Power Demands
Laboratory simulation has demonstrated a ~1% efficiency gain due in part to NXP’s High Voltage Gate Driver’s dedicated feature. This feature provides designers the ability to dynamically adjust the strength of the gate drive signal based on real-time operating conditions, achieving a balance between efficiency, switching speed, and electromagnetic performance. According to some Worldwide Harmonized Light Vehicle Test Procedure (WLTP) models, this could translate into a 14 mile increase in extended range compared to traditional EV solutions.
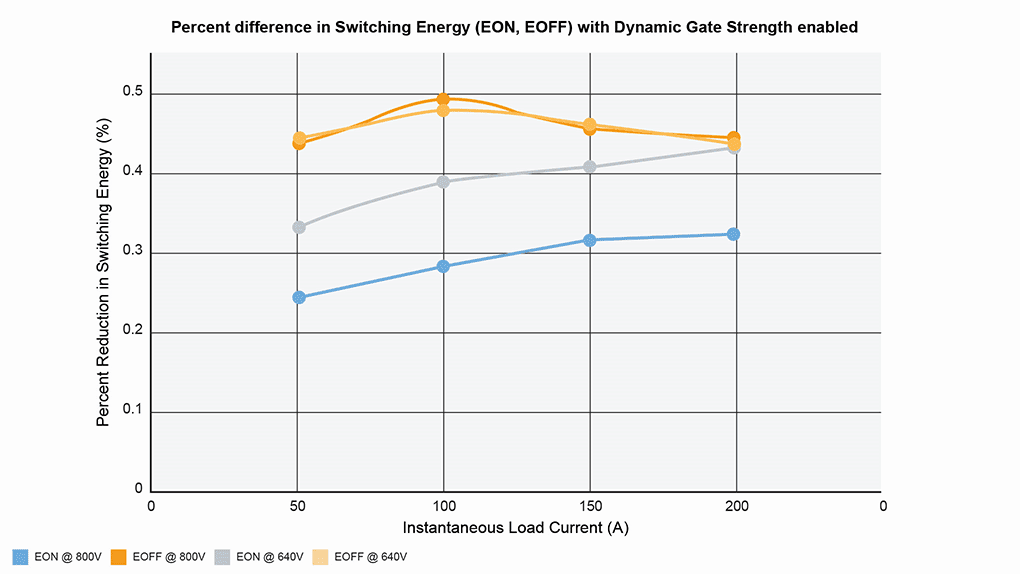
Designed with functional safety in-mind: Beyond device collateral, system FuSa collateral
When it comes to functional safety (FuSA), compliant components prioritize high quality and reliability. The approach to safety is reflected in every step from design to manufacturing, to documentation and support. ASIL D components compliant with the highest risk level, such as NXP’s S32K396 MCU, FS2633 system basis chip and GD3162 high-voltage gate driver, are used in the EV Traction Inverter Reference Design. To ease customer integration, some FuSa documentation are also proposed including System Safety Concept which explains Safety requirements from assumed safety goals to the hardware and software level.
Designed for reliability and life-long durability: YM SiC power module
800 V traction inverter requires a silicon carbide solution. Intrinsically SiC material is more reliable and durable than traditional silicon IGBTs. Wolfspeed saw an opportunity to integrate advanced packaging technology into their automotive qualified YM package to deliver further enhanced system durability,
The 1200 V six-pack YM SiC power module is designed with a direct-cooled copper pin fin baseplate, providing straightforward system assembly with enhanced thermal performance with pin fins directly submerged into the coolant. System operating temperatures are lowered with a Silicon Nitride substrate, a robust ceramic with excellent thermal shock and wear resistance, as heat is efficiently dissipated from the die. Another innovative packaging feature is sintered die attach, a state-of-the-art die attach technique creating a robust bond between the die and silicon nitride substrate, once again ensuring excellent heat conductivity and mechanical durability to enable higher power and superior thermal cycling performance. Both direct-cooled copper pin fin and sintered die attach technology improve thermal performance and system lifetime.
YM modules replaced traditional wire bonds with a copper top side clip to improve module ampacity, power cycling lifetime, and enable an optimized terminal layout, minimizing package inductance to reduce voltage overshoot and achieve ultra-low switching loss. To reduce potential mechanical failures, the automotive grade YM module is equipped with hard epoxy encapsulation – Epoxy mold compounds are replacing gel-based encapsulants, providing superior moisture resistance and structural integrity. The combination of sintered die attach with copper clip and epoxy mold compound enables up to 3× increase in lifetime compared to the closest competitor.

These advanced packaging technologies help the AQG324 qualified YM3 power module alleviate concerns operating in a harsh automotive environment – enabling consistent performance with unmatched durability.
Conclusion
NXP and Wolfspeed’s 800 V Traction Inverter Reference Design marks a pivotal advancement in the automotive industry’s transition to electric vehicles. This reference design addresses key challenges facing EV designers including improving efficiency, functional safety, and long-term reliability, ensuring that electric vehicles can match or exceed the performance of internal combustion vehicles. With features like dynamic gate strength adjustment and advanced silicon carbide power modules, the reference design is an essential tool to designers committed to delivering high-quality, efficient, and safe electric vehicles, ensuring performance across the lifetime.