Beat the Heat This Summer with Wolfspeed SiC in Residential & Commercial Air Conditioners and Heat Pumps
Article
Introduction
Silicon carbide is revolutionizing the heat pump and air conditioning industry by delivering unprecedented efficiency, enhanced durability, and superior performance in the most challenging of environments. Increasing global temperatures necessitate stricter efficiency regulations, which SiC powered solutions can achieve with either minimal retrofitting of existing designs or completely new system designs. This article will guide you through the technical considerations and practical applications of SiC discrete solutions and power modules in both residential and commercial heat pump and air conditioner designs.
Increasing efficiency standards driving system evolution
In the United States, the efficiency of heating and cooling systems is measured based on a national standard called the Seasonal Energy Efficiency Ratio (SEER). Beginning in 2023, all new residential central air conditioning and air source heat pump systems sold in the United States were required a SEER (Seasonal Energy Efficiency Ratio) rating of no less than 14 in the northern states and 15 SEER in the southern states, where cooling consumes a larger share of home energy use.
Similar standards exist in Europe called ESEER (European Energy Efficiency Ratio) that push new systems to be rated B or above to stay competitive in an energy conscious market. China has GB21455 Efficiency Standards pushing new designs to aim for higher efficiency grades but no lower than 5.
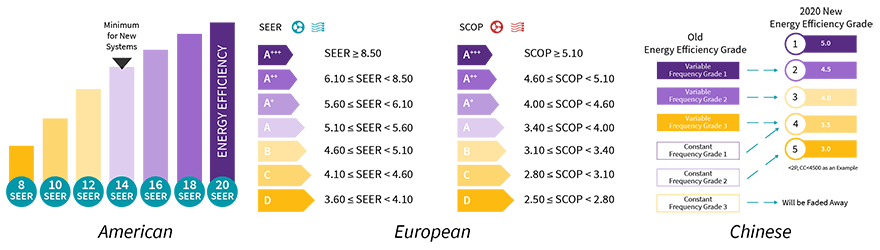
Figure 1 illustrates the increasingly strict standards in the U.S., Europe and China. Meeting these requirements is difficult for legacy power semiconductor devices. Silicon carbide provides a simple, cost-effective way to meet these standards while enabling smaller, more power dense and quieter overall heating and cooling systems.
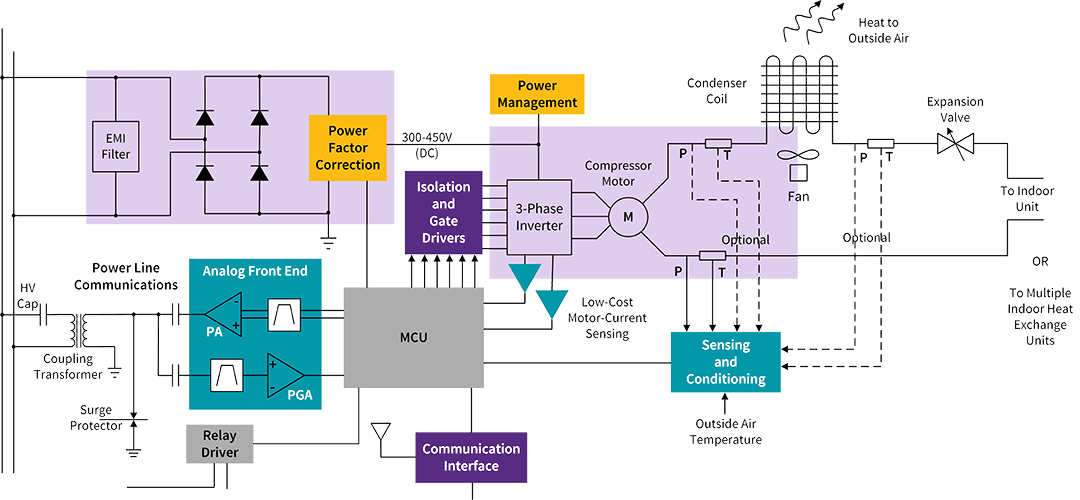
Improving efficiency with simple drop-in silicon carbide devices
Silicon carbide discrete devices can be easily integrated into existing heat pump and air conditioner designs enabling sufficient gains in efficiency to meet SEER, ESEER and GB21455 standards. Figure 2 illustrates the various subsystems of heat pumps and air conditioners including power conversion (PFC) and inverters, which together work to power the compressor and provide desired air temperature.

Figure 3 shows the typical silicon-based PFC in an active boost configuration and how it can be easily improved by simply replacing the silicon diode with a 650 V or 1200 V (depending upon the DC bus voltage) silicon carbide (SiC) Schottky diode without any system redesign. This is a very popular upgrade and yields around 0.5% or even higher increase in efficiency.
Wolfspeed’s 650 V and 1200 V Schottky diodes offer zero reverse recovery charge (Qrr) when compared to silicon diodes. Wolfspeed ’s C4D 1200 V and C3D 650 V SiC diode series provides the best reverse recovery performance when compared to any Si diodes in the market (Fig.4).
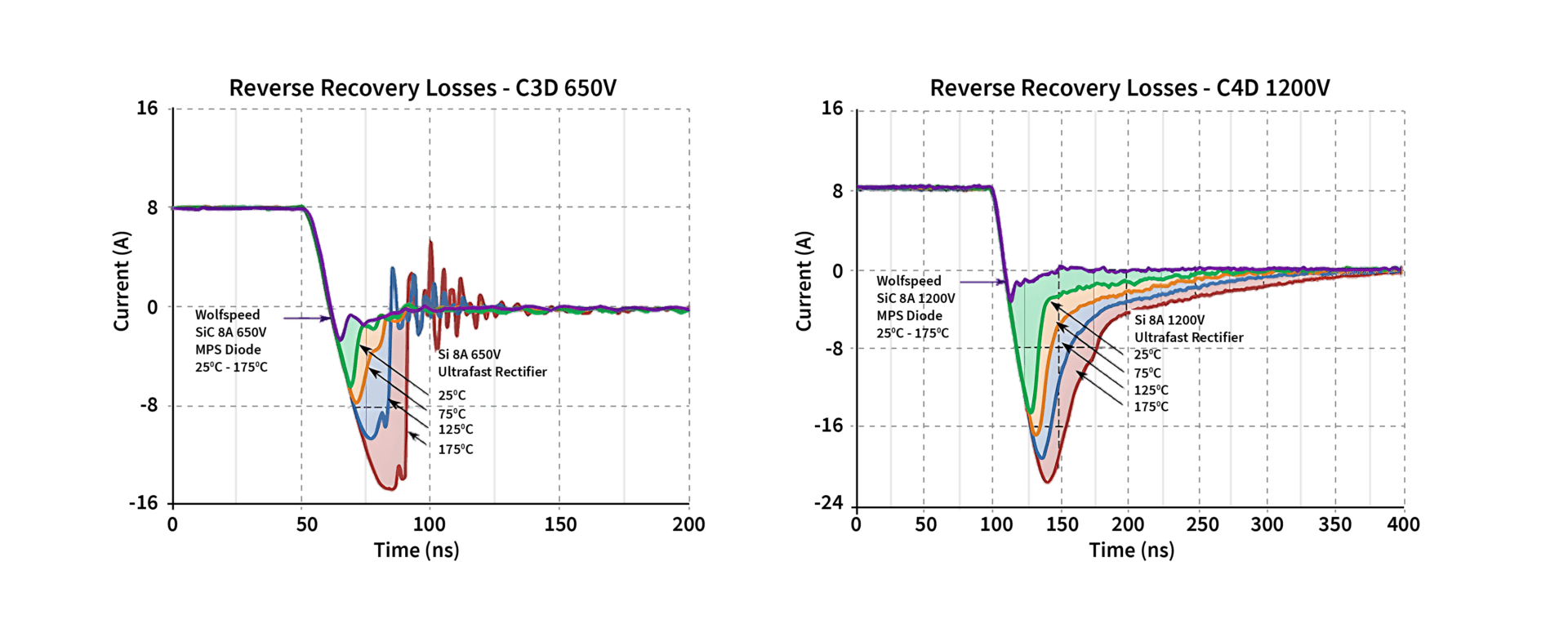
Redesigning with SiC Realizes Further Efficiency Gains
The performance benefits of silicon carbide can be further maximized by redesigning the PFC in a semi-bridgeless or bridgeless totem pole configuration (Fig. 5).
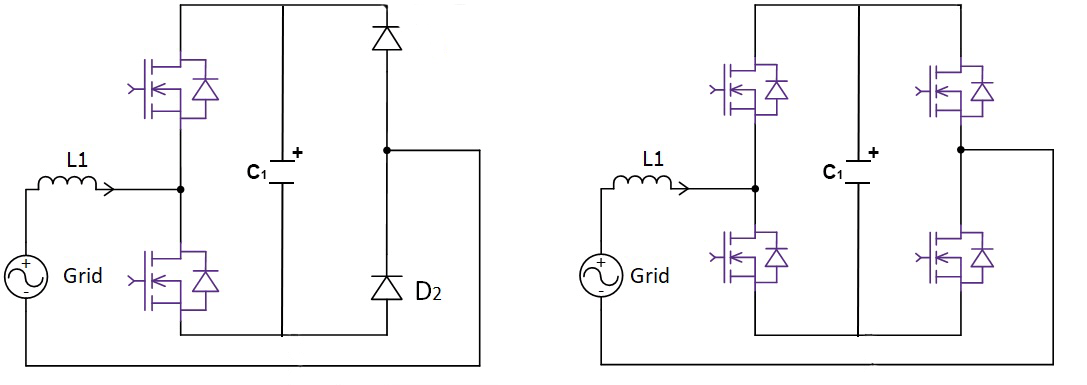
Implementing a semi-bridgeless PFC topology by using two SiC 650/750 V MOSFETs on the fast-switching leg along with two SiC 650/1200 V diodes for the slow switching leg (depending upon DC link voltage) can improve the system efficiency by 1.5% over a silicon-based boost PFC.
Similarly, a full bridgeless PFC topology using all SiC MOSFETs on both the fast and slow switching leg can improve system efficiency by 1.9% over Si based boost PFC. For reference, in a 11 kW compressor system switching at 16 kHz (Fig. 6), the total losses of the system can be reduced more than 50% when using SiC compared to a Silicon-based solution.
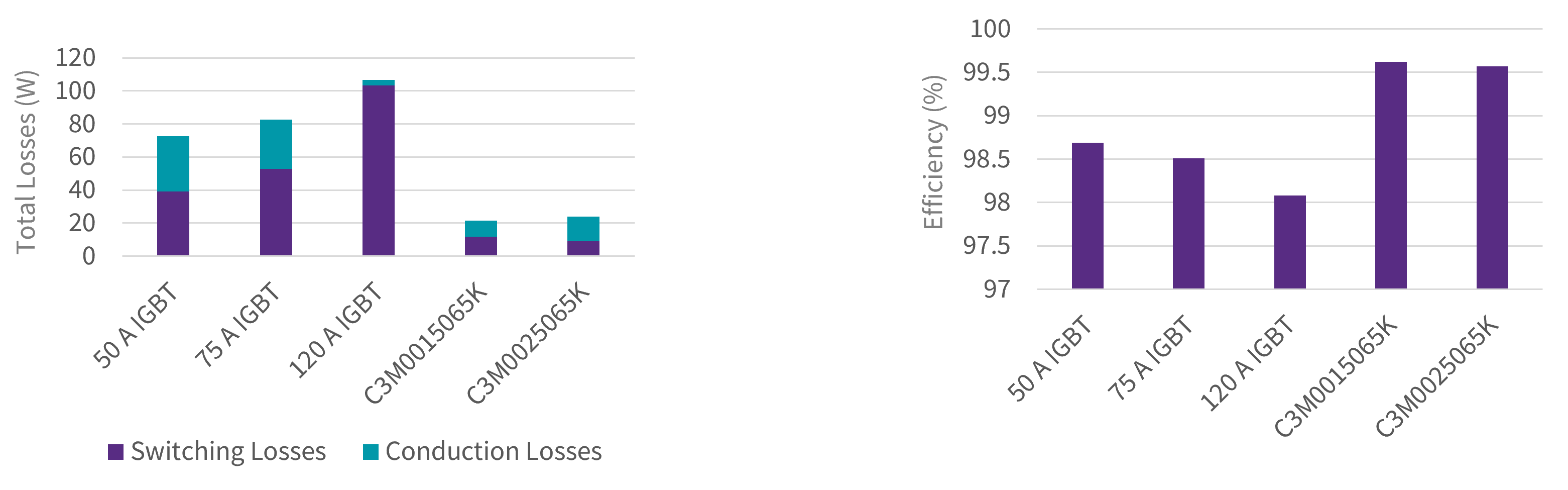

Silicon MOSFETs are not well suited to bridgeless PFC topologies due to their large reverse recovery (Fig. 7), and silicon IGBTs exhibit high switching losses, requiring lower switching frequencies and larger magnetic components resulting in a more costly solution.
Thanks to an improved switching performance and better thermals, this redesign approach reduces the audible noise and easily transitions new industrial motors installations from (International Efficiency) IE3 to IE4 and IE5 regulation as per IEC60034-14 standard (Fig 8).
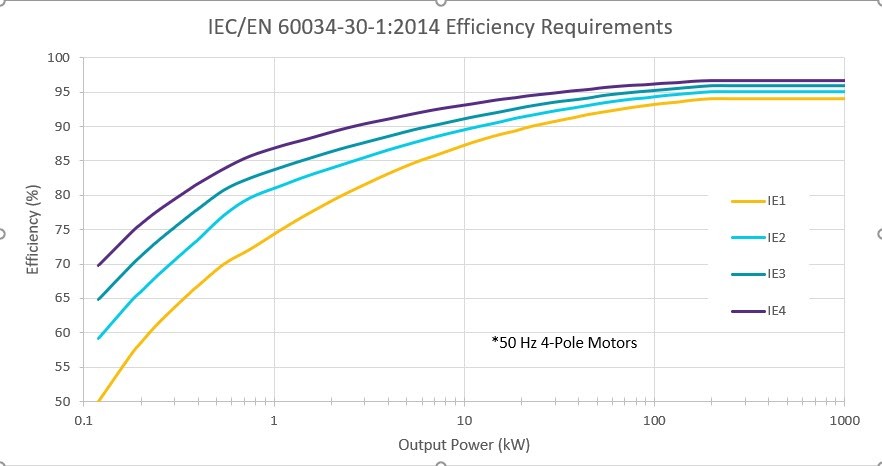
Additional gains in the inverter stage redesign
The inverter stage comprising of 6 switches can be easily upgraded into a full SiC solution by replacing all the existing IGBT switches (Fig. 9).
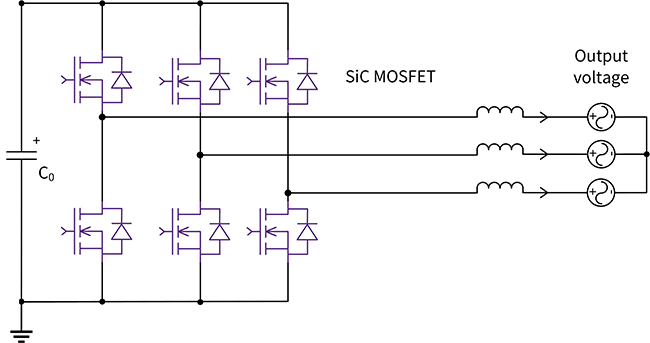
Wolfspeed’s SiC MOSFETs deliver the lowest conduction losses when compared to typical IGBT solutions. The figure below illustrates conduction losses for a 1200 V Wolfspeed SiC MOSFET vs a legacy IGBT. At a low load SiC MOSFETs deliver a 50% reduction in losses at a 30% load and 30% reduction in conduction losses at a half load (Fig. 10).
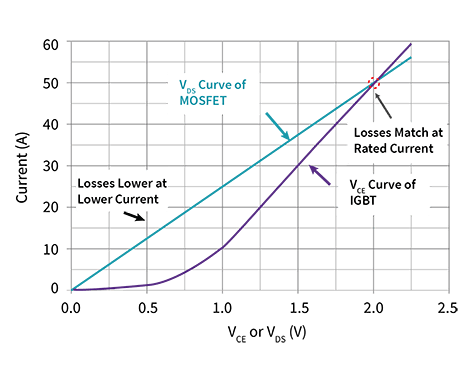
When a 1200 V SiC MOSFET’s switching is compared with a typical 1200 V IGBT, the advantage of ultra-low switching loss is evident as there is no trail current visible during turn off. This feature of a SiC MOSFET in turn provides up to 95% lower turn off switching losses or 85% overall total switching losses (Fig. 11).
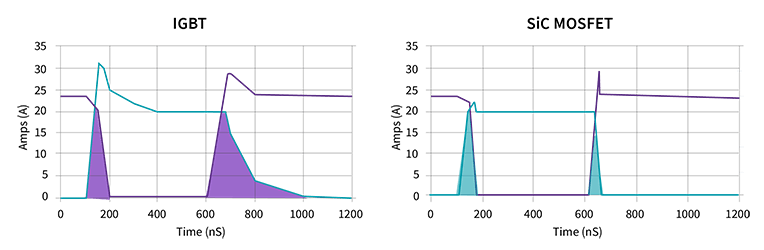
Additional savings with reduced Heatsink
In addition to consuming less power, SiC enables smaller and less expensive cooling designs in heat pumps and air conditioners due to improved thermal performance. For a 25 kW inverter operating at 8 kHz, using Wolfspeed’s 6 switch WolfPACKTM module compared to a similar IGBT modules leads to an overall 77% size reduction in the heatsink (Fig. 13) along with 1.1% improved efficiency. This is on inverter side alone, and when combined with a SiC powered Totem Pole PFC, a combined efficiency of 2.6% can be observed (Fig. 12).
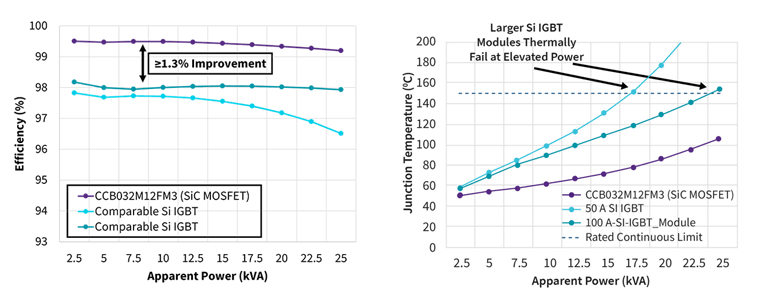
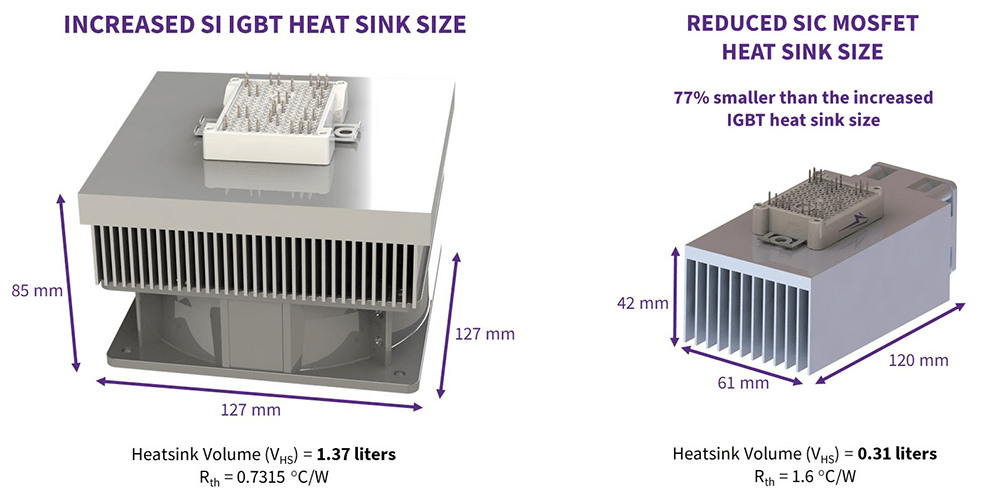
SiC based inverters provide a significant reduction in system-generated heat, enabling designers to use smaller heat sinks and design overall smaller, lighter compressors for air conditioners and heat pump systems.
Design support tools to lower the barrier to entry with SiC
Wolfspeed offers a suite of design support tools tailored to heat pumps and air conditioning that can help lower the barrier to entry when designing with SiC and speed your overall system optimization process.
Wolfspeed’s recently released 11kW High Efficiency Inverter reference design (CRD-11DA12N-K) (Fig. 14) features Wolfspeed’s 75 mΩ 1200 V MOSFETs and provides a perfect platform to test the advantages of SiC in heat pump and air conditioning compressor inverters. This design is characterized for thermals, inductance and circuit operation and features a simple 2-level, 3-phase topology with customizable firmware.
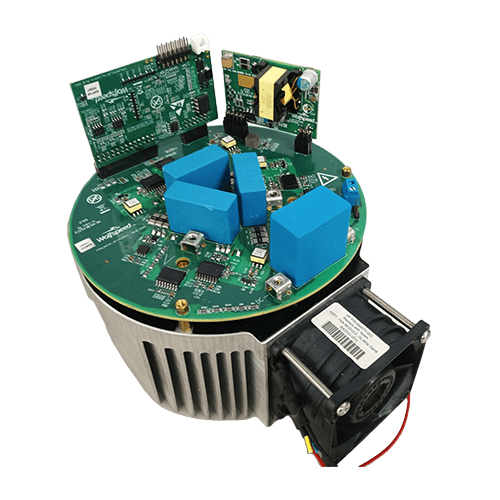
This inverter design can easily be upgraded to 20 kW by using Wolfspeed’s 40 mΩ C3M0040120K. When compared to an IGBT solution, the SiC solution outperforms an IGBT solution by up to 1.7% efficiency gains at 16 kHZ and up to 3.5% efficiency gain at 32 kHz, even when operating at lower dv/dt values to protect the motor (Fig. 15).
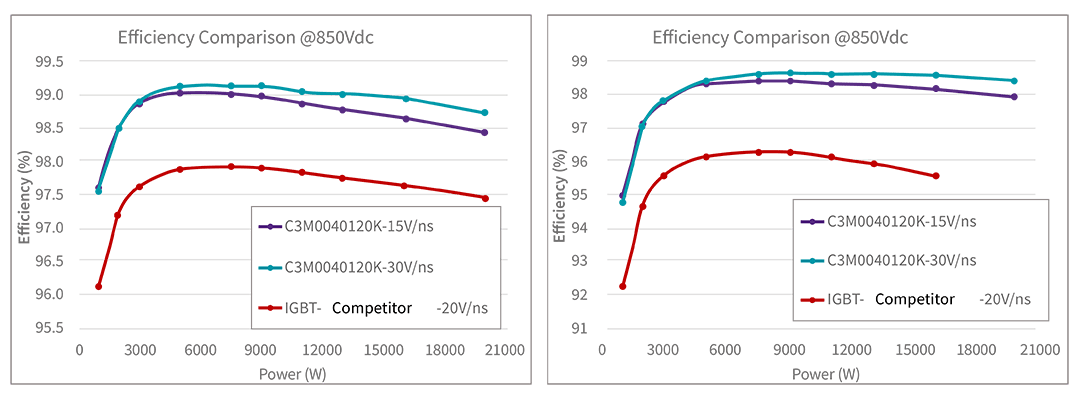
Building upon Wolfspeed’s SpeedValTM Kit Modular Evaluation Platform, the newly released Three-Phase Motherboard further speeds the transition from silicon to silicon carbide with a flexible set of building blocks for in-circuit evaluation of system performance. Designed with industrial motor drives, heat pumps and air conditioning systems in mind, SpeedVal Kit enables designers to rapidly evaluate and optimize silicon carbide MOSFETs paired with gate drivers from industry-leading partners. The 3-phase motherboard also enables precise control and firmware development with flexible control options to test simple static loads or advanced motor control function.
Savings & Environmental Impact
The environmental impact from upgrading heating and air conditioning systems with SiC in just the PFC and inverter is significant. For reference, with a three-phase 11 kW system, the consumer can expect to save at least 453 kWh of energy annually, or about €168 euros and more than offset any increase in system cost. These savings are especially significant when you look at the lifetime use of the unit. Assuming the system lasts 15 years, consumers will save 6800 kWh totaling around €2,520 euro. This also translates to 4.8 Metric tons of less CO2 * being released into the atmosphere, making SiC a more sustainable choice for designing next generation heat pumps and air conditioners.
General design recommendations for cleaner layout
- Designers are recommended to avoid overlapping between gate driver circuit and the drain of the MOSFET (Fig. 16a). This helps in reducing the risk of inducing external Cgd in the gate drive power loop. Benefits include:
- Lower switching losses
- Reduced risk of gate oscillation
- Lower EMI
- Keep sensitive signals away from the high dv/dt traces. Reducing the size of switching node traces minimizes parasitic capacitance to the DC bus, which reduces switching losses and EMI concerns. (Fig. 16b)
- Minimize the gate loop for the gate driver circuit as much as possible and place the external Cgs cap as close as possible to the MOSFET.
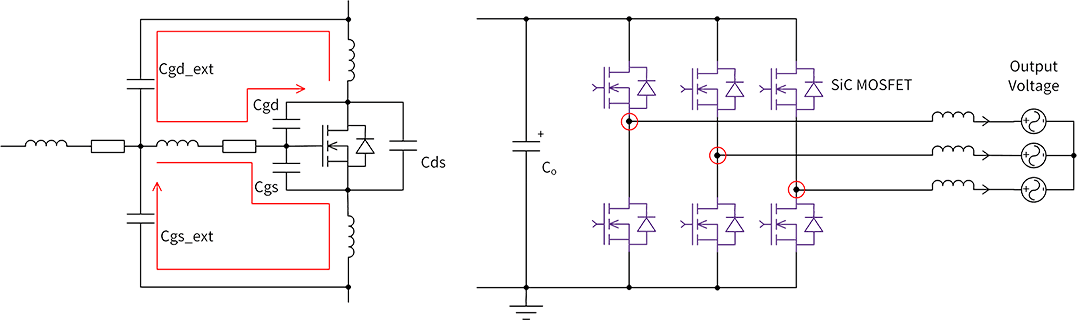
*(www.epa.gov)
Summary
With the rise in global temperatures there is an ever-increasing need for greener solutions to combat climate change. As demonstrated, SiC is a more sustainable choice when designing the next generation of heat pumps and air conditioners residential, industrial and commercial applications.
Designing with SiC has never been easier with Wolfspeed’s 11kW High Efficiency Inverter reference design (CRD-11DA12N-K) that can be powered up to 20 kW acting as a guiding tool to unleash the power of SiC and surpass new efficiency standards with ease. You can even simulate your design challenges today with our online SpeedFit™ Design Simulator, quickly prototype and test using the SpeedVal evaluation platform, or connect directly with our silicon carbide experts at our Power Applications Forum.