Designing with Top Side Cooled (TSC) Silicon Carbide Power Devices
Article
Improve thermal management and conserve power with Wolfspeed’s New TSC MOSFETs and Schottky diodes, coming soon.
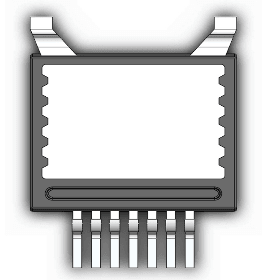
Applications:
- Electric Vehicle (EV) On-Board Chargers and Fast Charging Infrastructure
- EV & Industrial HVAC (Heating, Ventilation, and Air Conditioning) Motor Drives
- High Voltage DC/DC Converters
- Solar and Energy Storage
- Industrial Motor Drives
- Industrial Power Supplies
Features:
- JEDEC & AEC-Q101 Qualified Options
- Low profile, surface mount footprint
- Top side cooling with low Rth
- SiC MOSFETs Available from 750V - 1200V
- SiC Schottky Diodes Planned from 650V - 1200V
Benefits:
- Highest Creepage Distance Available for SiC Top Side Cooled Packages
- Higher System Power Density with Optimized PCB Layouts
- High Volume Manufacturing Capability with Surface Mount Footprint
What’s New? Advantages of New Top Side Cooled Packages
Most standard surface mount discrete power semiconductors remove heat through the bottom of the device by making direct contact with the power circuit board (PCB), which utilizes a heat sink or cooling plate attached underneath. This method is common across many different power electronics applications, particularly when size and weight requirements do not limit PCB mounting and heat sinks.
Top side cooled (TSC) devices, on the other hand, dissipate heat through the top side of the package. Inside TSC packages, the die sits upside down in the upper portion of the package to allow heat to flow directly to the top surface. Generally, TSC devices are best suited for high-performance applications such as automotive and e-mobility systems where high-power densities, advanced thermal management solutions, and small footprints are essential. Within these applications, TSC devices help address cooling requirements by enabling maximum power dissipation and optimizing thermal performance.
TSC designs also allow for dual-side usage of the PCB since the bottom board surface is no longer needed for the heatsink interface. Removing the heatsink from the thermal path not only creates an improved overall system thermal impedance; it also allows for automated assembly, which can increase manufacturing throughput for a more efficient and cost-effective solution.
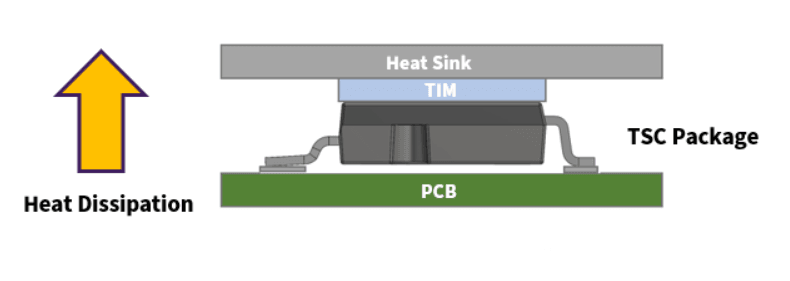
Evaluating U2 TSC Devices Made Easy with SpeedVal™ Kit
Wolfspeed’s SpeedVal Kit Modular Evaluation Platform allows engineers to reduce the transition from silicon to silicon carbide (SiC) with a flexible set of building blocks for in-circuit evaluation of system performance at real operating points. The recently released 3-phase motherboard enables high-power testing with static loads as well as a foundation for advanced motor control firmware development.
Evaluation boards for a variety of Rdson ratings for Wolfspeed’s TSC MOSFET devices are coming soon.
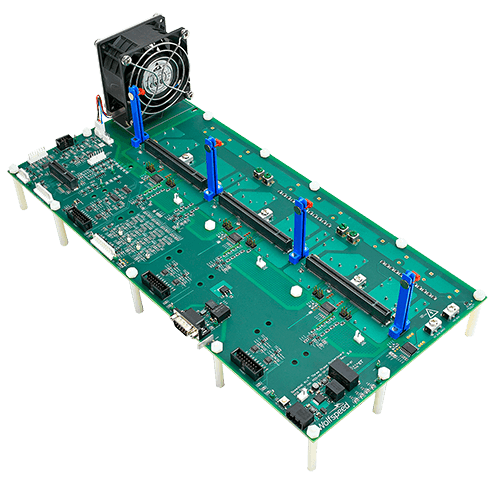
Putting U2 TSC Devices to Work: 13 kW Automotive HVAC Motor Drive Reference Design
Wolfspeed’s upcoming 13 kW motor drive reference design, featuring the TSC U2 package, demonstrates the benefits of U2 devices for 10 kW+ EV HVAC systems, which support thermal management of the cabin, battery, and electronics. Optimizing the efficiency and operating temperature range of the HVAC system with the implementation of SiC enables systems designers to bring fast charging to the driver in under 15 minutes, while also extending the driving range per charge for the lifetime of the car. Utilizing Wolfspeed's new CRD-13DA12N-U2 13 kW HVAC reference design, SiC enables:
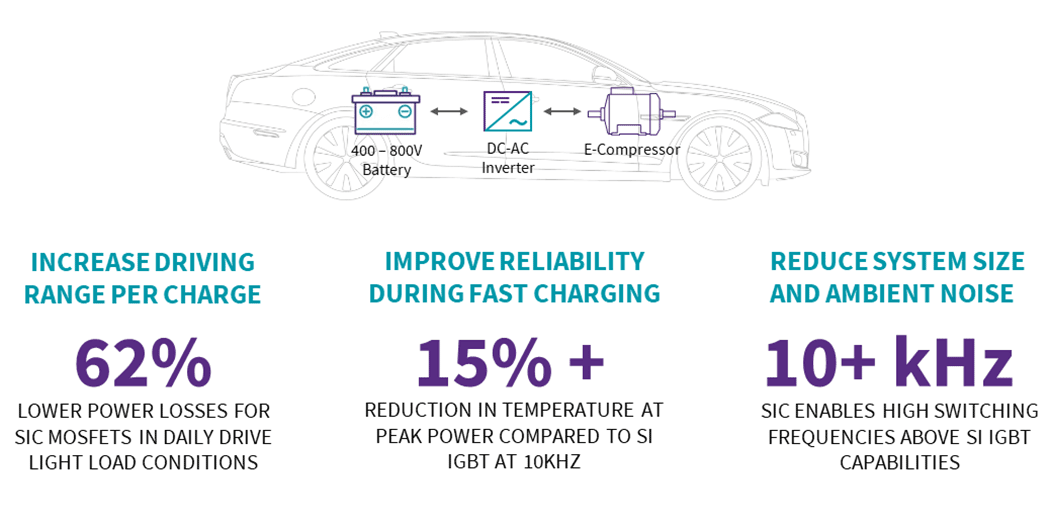
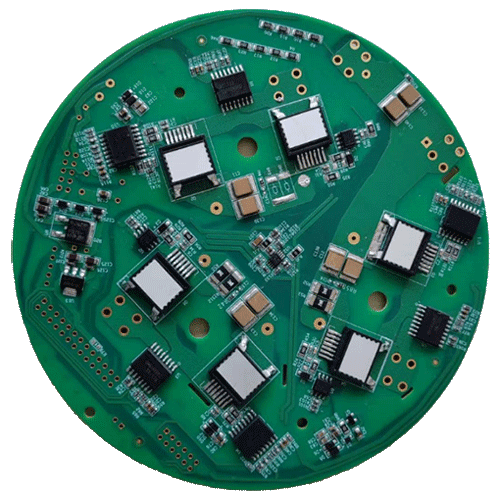
Reference Design Specifications:
- Input Voltage: 550 – 850 V
- Max Output Current: 25 A
- Max Output Power: 13 kW
- Switching Frequency: 10 – 32 kHz
- Peak Efficiency: > 98%