Medium power applications are the sweet spot for Wolfspeed WolfPACK™ power modules
Article
With the increasing adoption of power electronics, design engineers are constantly challenged to create systems that are more efficient than the previous ones. Selection of the optimal component for a new design can often be a major challenge but doing so is critical for meeting converter specifications without unnecessary system costs. At Wolfspeed, we understand this challenge and are consistently adding new products to our portfolio which can better address our customer’s needs. Our objective is to provide a wide range of products that application engineers can implement to make their designs more efficient, robust, and configurable than their competitors’.
With over 30 years of Silicon-Carbide (SiC) research and development, our current portfolio includes a variety of SiC Schottky diodes, MOSFETs, and power modules which cover a wide range of power requirements. When compared to Silicon (Si) transistors, the superior ampacity and reduced switching losses lead to greater converter efficiency and power density. This ultimately provides an optimal solution for medium power converters (10 to 100 kW). Because of this, Wolfspeed has recently launched the WolfPACK™ power module family. These modules are an ideal replacement for converters which would traditionally require implementing parallel discrete devices.
Power modules versus discrete transistors
In medium power applications, discrete implementations generally require multiple devices per switching node. Whether in parallel or interleaved, these additional devices further increase the design challenges of layout, thermal management, isolation, electromagnetic-interference (EMI), and reliability. The key advantage offered by power modules is that they are engineered to reduce the complexity of these challenges and (especially when replacing an array of discrete transistors) can greatly reduce the system design burden.
Typical discrete design challenges for medium power systems
When designing a discrete component converter, designers must carefully consider the transistor specifications required (such as blocking voltage, current rating, on-state resistance, and switching energies). Device selection is typically a substantial design problem, and, due to packaging limitations, discrete devices limit scalability. This means that increasing system power requirements, or designing a higher output variant of a converter, will generally require substantial redesigns. Additionally new, higher voltage/current transistors would be required with a repeat of device selection. New thermal management, PCB layout, and mechanical designs will often be required to accommodate the package.
If the path of incorporating additional transistors in parallel is chosen instead, this presents a new set of challenges. For example, additional space will be required for the new devices, their thermal management, and peripheral components (such as gate drives and passives). Additional layout challenges will be created as imbalanced inductances between parallel transistors can lead to higher losses, voltage overshoot, and reduced lifetime. In other words, substantially scaling the output power of a discrete converter can be as challenging as designing a new converter.
As converters target ever higher switching frequencies in order to achieve a greater power density, the challenges of designing a discrete also increase. The faster slew-rates necessary to achieve high switching frequencies can induce EMI into the control system, especially if the PCB is poorly designed. The immediate threat of EMI is inducing transistor turn on which can cause additional losses, reduced device lifetime, or even converter failure. These faster slew-rates also increase gate driver cost, as substantial isolation is required to protect the sensitive control system from the power transients. Such gate drive costs are also correlated to the number of parallel transistors required.
Avoiding common failure modes for medium power designs: Reducing stray inductance
Reduction of stray inductance is critical to converter design. PCB traces, packaging, connectors, interfaces, leads, and wires all contribute inductance and the power and gate loops must be carefully designed. Especially critical is the inductance which couples gate and power loops together, common to the power-source and signal-source connections (i.e. common source inductance). Packages which offer a separate kelvin connection are generally preferred as they can eliminate any external LCS. While these considerations have always mattered in converter design, but when utilizing the high di/dt of SiC transistors, these inductances play an even more critical role. This is because the di/dt generated by MOSFET switching will induce a voltage across the parasitic inductances (VL = L × di/dt), which increases voltage peaks at the MOSFET drain. Therefore, the margin required between bus voltage and MOSFET blocking voltage is directly correlated to switching speed and parasitic inductance. Since switching speed is also correlated to switching losses, it is far more beneficial to reduce parasitic inductance than switching speed. These effects become worse when paralleling devices, as significant current imbalance can occur during switching transients.1
Power module implementations eliminate many of these design challenges, optimization of power and gate loops becomes easier as much of the necessary engineering is already accomplished within the modules. This reduces the converter design complexity and simplifies alterations to layout. Designers can also find reliable rules of thumb for module layout in Wolfspeed’s Design Library.2
Avoiding common failure modes or medium power designs: Simplified thermal management
Discrete devices generally require voltage isolation between their thermal interface and the thermal management system. This is because the heatsink or cold-plate will be grounded, while the discrete component will be exposed to high voltages. Power modules remove the need to design additional insulation by mounting the devices to a suitable ceramic with copper planes (generally referred to as direct-bonded copper or DBC). The traditional stack-up used in power module design is to then attach this DBC to a metal (or composite) baseplate, which includes mounting points for bolting the module onto a heatsink or cold-plate. Care must be taken in mounting the baseplate as uneven pressure or insufficient / excessive thermal interface material (TIM) cancan increase thermal resistance between the module and thermal management system.
There are two main factors required for good thermal transfer between these interfaces: thermal resistance (Rth) and the coefficient of thermal expansion (CTE).
The Rth is a model of how easily heat is transferred from one interface to another — higher Rth indicates that less thermal energy (or power loss) can be extracted from the heat source. The value of thermal resistance depends on the contact area, thermal conductivity of the material, and thickness of the layer. In a power module with baseplate, the RJC, or thermal resistance between the transistor junction and the case (baseplate), as well as the thermal resistance between the case and the heatsink must be considered. In order to reduce RJC, the new Wolfspeed WolfPACK modules eliminate the baseplate and allow direct cooling of the DBC substrate. This enables increased heat transfer from the transistor, reducing the junction temperature of the chip for a given power level (Figure 2).
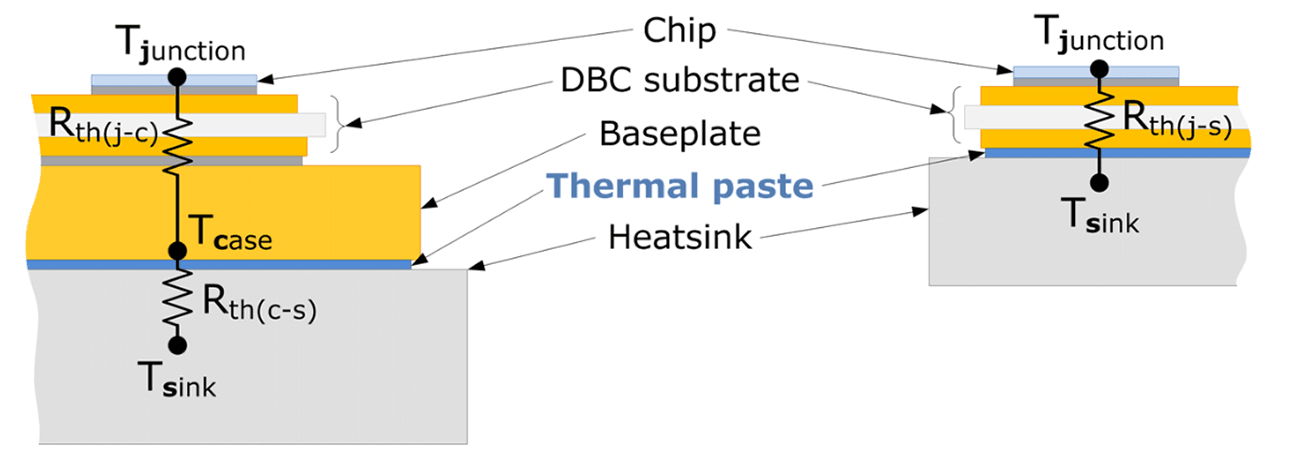
Typically, the CTE of a SiC die (4.0 10–6/K) is matched to the CTE of the ceramic substrate, which is normally composed of aluminum nitride (AlN: 4.5 10–6/K) or aluminum oxide (Al2O3: 8.2 10–6/K). The baseplate, however, is generally made of either copper (Cu: 16.5 10–6/K) or an Al-SiC composite (8.4 10–6/K) for mechanical reasons. This mismatch, coupled with the inflexible bond layer between the DBC and ceramic, can cause increased stresses at joints of these materials. These thermomechanical stresses acting on the large interface between the DBC and baseplate can cause solder fatigue and fractures. Sufficient thermal cycling can cause delamination of the solder joint (which greatly increases thermal resistance) or even fracture the brittle ceramic DBC, leading to module failures.4,5
The unique, baseplate-less design of the Wolfspeed WolfPACK eliminates this mechanical failure point by eliminating the inflexible connection to the mismatched material. The baseplate mounting bolts are replaced by metal tabs which pull on the plastic housing, evenly distributing the force across the substrate. As the interface between DBC and heatsink is flexible grease (rather than rigid solder), it can allow differential expansion between materials without inducing substantial stress. In addition to the reliability advantage over manual and automatic soldering (refer to Table 1), these press-fit metal tabs greatly reduce cost of assembly for power modules. This mounting approach simplifies thermal system design as it facilitates mounting any number of modules and other components to a singular heatsink or cold-plate.
Process | Conductor Diameter (mm2) | Failure Rate λ ref in FIT(1) | Notes: Standards/Guidelines | |
---|---|---|---|---|
Solder | Manual Automatic | - | 0.5 0.05 | IPC 6102, class 2 |
Press-Fit | 0.3 to 2 | 0.005 | IEC 60352-5 | |
Wire Bonding for hybrid circuit | Al Au | - | 0.1 0.1 | 28 µm / wedge bond 25 µm / wedge bond |
Winding | 0.05 to 0.5 | 0.25 | DIN EN 60352-1 / IEC 60352-1 CORR1 | |
Crimping | Manual Automatic | 0.05 to 300 | 0.2 | DIN EN 60352-1 / IEC 60352-2 A 1+2 |
Clips | 0.1 to 0.5 | 0.2 | DIN 41611-4 | |
Insulation Piercing Connectors | 0.05 to 1 | 0.25 | IEC 60352-3 / IEC 60352-4 | |
Screws | 0.5 to 16 | 0.5 | DIN EN 60999-1 | |
Terminals (spring force) | 0.5 to 16 | 0.5 | DIN EN 60999-1 | |
1) 1 FIT = 1 x 10-9 1/h; (one failure per 109 component hours) 2) Acceptance conditions for PCBs |
TABLE 1: FAILURE RATES FOR VARIOUS CONTACT TECHNOLOGIES. (SOURCE: SIEMENS NORM SN 29500-5/EDITIONS 2004-06 PART 5)
How can a designer scale up power with the Wolfspeed WolfPACK?
The high-power/high-current capabilities of the Wolfspeed WolfPACK modules greatly simplify the design of medium power converters (up to 100 kW), the ease of implementations makes them more scalable, and small footprint allows for higher power-density when compared with discretes components and traditional power modules. Wolfspeed’s WolfPACK modules are available in a range of different specifications and configurations, which allows for rapid development of many power system types which are easily built and maintained but highly reliable in the field. With a maximum rated drain-source voltage (VDS) of 1,200 V and a DC continuous drain current (ID) ranging from 30 A up to 100 A, these modules can readily form the building blocks for medium power systems. Moreover, Wolfspeed’s WolfPACK modules are an extremely scalable solution as expanding a system through interleaving and paralleling is far simpler due to the module design.
Medium power DC/DC converters are necessary in a myriad of applications, including EV charging, solar energy transfer/storage, and power supplies. A multi-phase interleaved, bidirectional DC-to-DC converter, for instance, can be achieved by connecting an arbitrary number of power phase legs in parallel to scale the maximum output current/power capability while reducing current ripple (Figure 3). The gate signals for the switches of a three-phase interleaved DC/DC converter are phase shifted by 120° for the cancellation of low-frequency harmonics. An interleaving can be achieved with only minor alterations to the controller and thermal system. The output power can reach 60+ kilowatts and still be well below the maximum junction temperature of the SiC die, allowing for the system to function reliably over its operational lifetime. Interleaving is a good strategy to avoid some of the challenges of paralleling devices, while also improving system performance and reducing output inductor size.
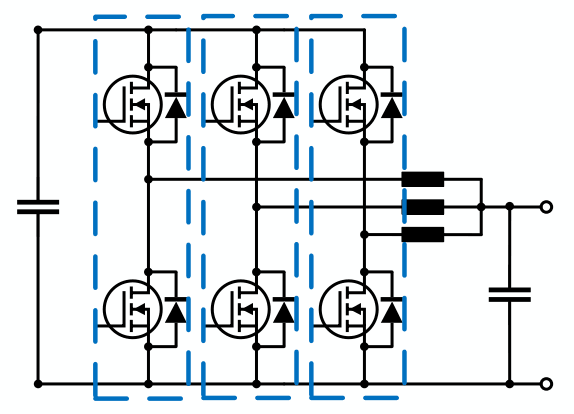
This same interleaving methodology can be applied to a variety of converter and inverter architectures to reliably scale up power without sacrificing electrical and thermal performance. Coupled with the benefits of SiC technology and the simplified thermal management of the baseplate-less Wolfspeed WolfPACK family, deployment of converter families with a wide output power range has never been easier!
Simple scalability is one of the defining characteristics of the Wolfspeed WolfPACK family of baseplateless power modules. As previously discussed, interleaving or paralleling modules is one way to increase the power capability of a system. However, one of the easiest ways to scale-up the power rating of your FM3-based system is as simple as now inserting the GM3 into your solution. But scalability isn’t just about power, it’s about options – options that could enhance the performance of your present solution depending on what you are trying to achieve with your scalable system.
To help understand what benefits inserting the GM3 could provide within your system, let’s consider the typical 2-level grid-tied inverter or AFE system shown below with the following parameters: 800 VDC bus voltage, 480 VAC line-to-line RMS grid voltage, an ambient temperature of Tamb = 50 °C, and line inductors of L = 100 µH. Each bridge-leg represents a half-bridge FM3 or GM3 Wolfspeed Wolfpack™ power module.
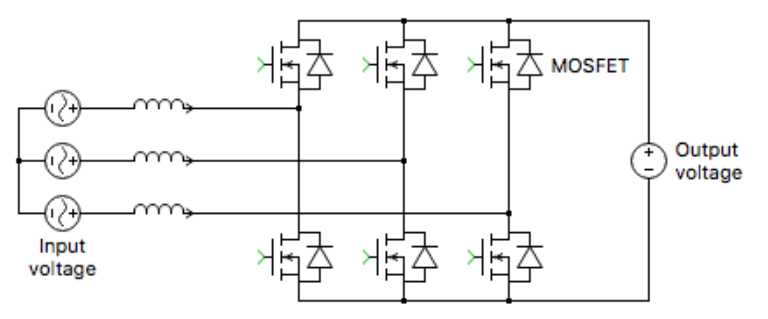
For this study, we’ll consider the CAB011M12FM3 (11 mΩ) as our baseline FM3-based solution. With the system parameters defined above and operating at a relatively high switching frequency of 50 kHz, a power rating of 75 kW can be achieved before reaching the maximum junction temperature of 150 °C due to the semiconductor losses.
Inserting the CAB008M12GM3 (8 mΩ) into the exact same 75 kW / 50 kHz system still demonstrates a very high system efficiency of 98.9%, but reduces the junction temperature of the devices to only 114 °C. Operating the devices at this reduced temperature can improve lifetime or reliability, or provide increased overhead and overload capability. Alternatively, it’s obvious there is room to increase the junction temperature and thus the power rating of the system, which in this case it could be increased to 100 kW (50 kHz / Tj = 150 °C).
Further performance enhancements could be made over the previously discussed systems by now inserting the CAB006M12GM3 (6 mΩ). Similarly, the operating junction temperature of the devices could be reduced for a given power rating, or otherwise the extra junction temperature margin can further be utilized by either increasing the power rating of the system or even increasing the operational switching frequency. A summary of this comparative study is given below to demonstrate the scalability options that the GM3 platform provides.
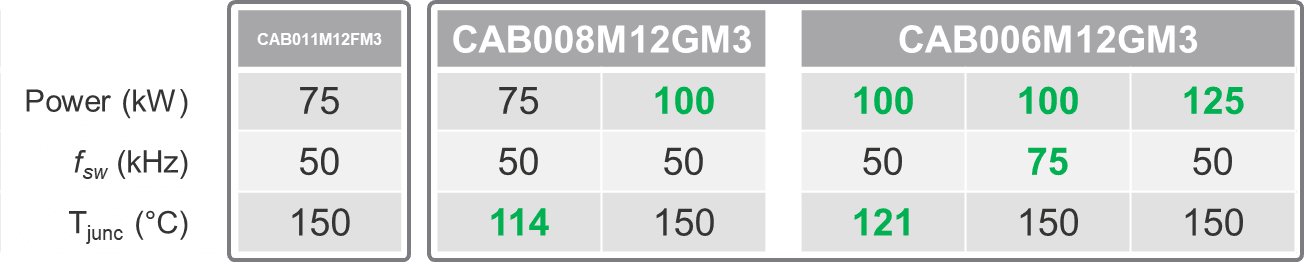
While it’s obvious that inserting the larger GM3 platform could increase the power rating of your FM3-based solution, as demonstrated, this isn’t the only benefit that it could provide to your scalable solution. Depending on your design goals, decreasing the operating junction temperature to increase robustness of your system, or increasing switching frequency to reduce magnetic component size/cost and improve control bandwidth both could be highly desirable performance enhancements for your scalable system. Regardless, the GM3 platform provides designers options to easily scale their power electronic system.
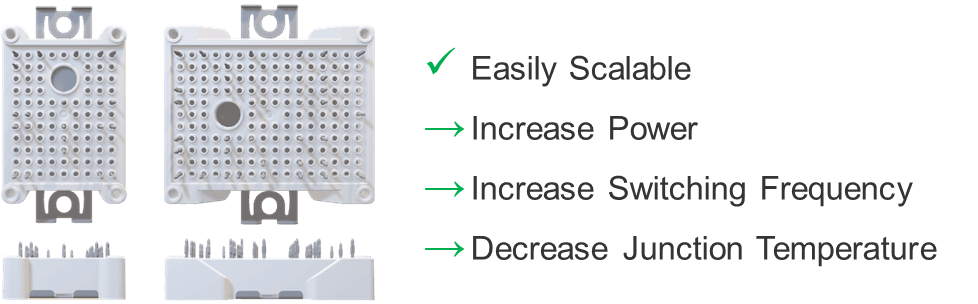
Beyond increasing module size or active die area, another tactic to promote scalability comes with the selection of the material stack-up of the power module. With no baseplate, there are really only two degrees of freedom for this selection, which both significantly contribute to the overall thermal resistance of the module – the thermal interface material (TIM) and the substrate ceramic material. As seen from the chart, the TIM layer can contribute up to 60% of the overall junction-to-heatsink thermal resistance (RthJH). While the end user has many choices when it comes to TIM selection, it is difficult to significantly impact TIM layer contribution, even with a very high-performance thermal paste material. The other degree of freedom, the ceramic substrate, however, can dramatically decrease the overall thermal resistance value as we will explore next.
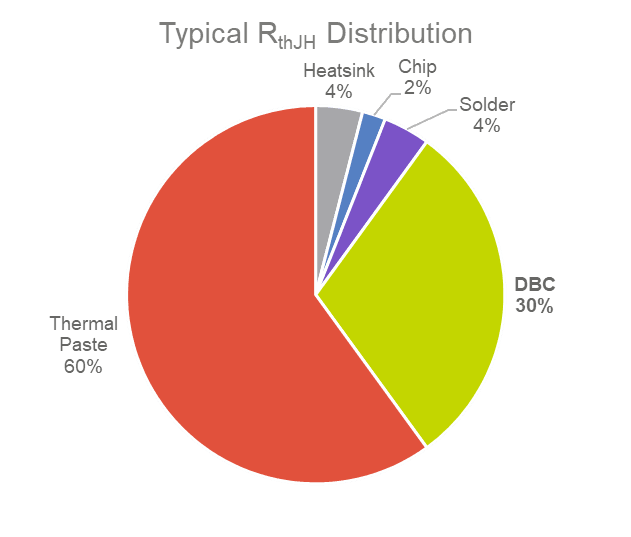
The typical go-to ceramic substrate for Wolfspeed WolfPACK family is aluminum oxide (Al2O3) as it provides a very nice cost-performance trade-off that suits this baseplateless module family well. However, customers understand that aluminum nitride (AlN) can offer large performance impacts with a relatively low-cost increase. With 7× higher thermal conductivity compared to Al2O3, the impacts can easily be understood: reduces thermal resistance, lowers Tj for given loss, enhances PC lifetime for given losses, enables higher utilization of SiC performance.
This is once again demonstrated by considering a 2-level grid-tied inverter operating at an 800 VDC bus voltage, 480 VAC line-to-line RMS grid voltage, an ambient temperature of Tamb = 50 °C, and line inductors of L = 100 µH. Like the previous scalability study, utilizing an AlN substrate for the 6 mΩ GM3 creates the ability to scale across the three variables: power, switching frequency, and junction temperature. This enables solutions for customers who need more usable ampacity, or in some use cases, reduce the operating junction temperature to enhance lifetime, or to enable higher heatsink temperature (cost reduction).
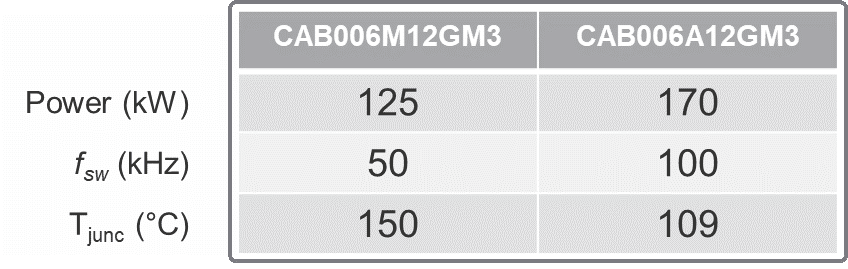
Wolfspeed WolfPACK offers a new design built on the history of silicon carbide technology investment
Wolfspeed’s WolfPACK power portfolio is the culmination of decades of investment in silicon carbide research and development, coupled with a baseplate-less design to give OEMs and design engineers the most choice to support use cases across a broad array of industry segments.
Greater flexibility and scalability for designers is made possible by housing several SiC MOSFETs inside a container that provides press-fit, solder-less pins to interface with an external PCB. The Wolfspeed WolfPACK family of power modules feature application-specific pinouts optimized based on the internal arrangement of the MOSFETs, such as half-bridge, full-bridge, six-pack, and buck/boost layouts. In lieu of a baseplate, the bottom of the Wolfspeed WolfPACK housing employs a ceramic substrate for an electrically isolated module bottom with metal mounting tabs which employ spring-force to interface with the heatsink. This approach distributes pressure evenly along the bottom of the module to ensure good thermal contact with the heatsink while providing a rigid and robust mechanical link between the heatsink, module, and PCB.
High power density in a small baseplate-less footprint, coupled with SiC technology enables compact layout, faster, cleaner switching, and affords designers as much as a 25% reduction in size. In addition to its power density advantage, Wolfspeed WolfPACK modules streamline system layout and assembly processes. This affords engineers working in the medium power applications the ability to maximize power density while minimizing design complexity.
The inherent simplicity of Wolfspeed WolfPACK supports a high level of scalability that helps to accelerate production pipelines and lowers system assembly costs while also providing a great deal of choice. These new Wolfspeed WolfPACK modules come in all SiC MOSFET half-bridge and all SiC MOSFET six-pack configurations with a variety of module resistance options.
Power modules that deliver choice and reliability
The new family of Wolfspeed WolfPACK modules deliver a power portfolio that encompasses a wide spectrum of applications for today’s designers, whether they’re working on single-kilowatt designs or megawatt systems — and anything in between.
Built on the backbone of Wolfspeed’s industry leading silicon carbide technology, these modules offer incredibly low losses in a small package that lends itself extremely well to automation and manufacturing at scale to provide clean, reliable power for energy conversion systems.
Please visit www.wolfspeed.com/wolfpack for more information and access to data sheets, material content, and application notes.
Featured Products
Wolfspeed WolfPACK™ Silicon Carbide Power Modules Family
Wolfspeed WolfPACK™ Silicon Carbide Power Modules Family
Wolfspeed WolfPACK™ Silicon Carbide Power Modules Family
Product SKU | Buy Online | Request Sample | Data Sheet | Package | Configuration | Blocking Voltage | Current Rating | RDS(ON) at 25°C | Generation | Tjmax | Module Size |
---|---|---|---|---|---|---|---|---|---|---|---|
CAB004M12GM4 New | GM | Half-Bridge | 1200 V | 200 A | 4 mΩ | Gen 4 | 175 °C | 62.8 x 56.7 mm | |||
GM | Half-Bridge | 1200 V | 200 A | 4 mΩ | Gen 4 | 175 °C | 62.8 x 56.7 mm | ||||
CAB5R0A23GM4 New | GM | Half Bridge (AlN substrate) | 2300 V | 200 A | 5 mΩ | Gen 4 MOS | 150 °C | 62.8 x 56.7 mm | |||
GM | Half Bridge (AlN substrate) | 2300 V | 200 A | 5 mΩ | Gen 4 MOS | 150 °C | 62.8 x 56.7 mm | ||||
GM | Half-Bridge | 1200 V | 200 A | 6 mΩ | Gen 3 MOS | 150 °C | 62.8 x 56.7 mm | ||||
GM | Half Bridge (AlN substrate) | 1200 V | 200 A | 6 mΩ | Gen 3 MOS | 150 °C | 62.8 x 56.7 mm | ||||
GM | Half-Bridge | 1200 V | 200 A | 6 mΩ | Gen 3 MOS | 150 °C | 62.8 x 56.7 mm | ||||
GM | Half Bridge (AlN substrate) | 1200 V | 200 A | 6 mΩ | Gen 3 MOS | 150 °C | 62.8 x 56.7 mm | ||||
CAB6R0A23GM4 New | GM | Half Bridge (AlN substrate) | 2300 V | 200 A | 6 mΩ | Gen 4 MOS | 150 °C | 62.8 x 56.7 mm | |||
GM | Half Bridge (AlN substrate) | 2300 V | 200 A | 6 mΩ | Gen 4 MOS | 150 °C | 62.8 x 56.7 mm | ||||
CAB7R5A23GM4 New | GM | Half Bridge (AlN substrate) | 2300 V | 170 A | 7.5 mΩ | Gen 4 MOS | 150 °C | 62.8 x 56.7 mm | |||
GM | Half Bridge (AlN substrate) | 2300 V | 170 A | 7.5 mΩ | Gen 4 MOS | 150 °C | 62.8 x 56.7 mm | ||||
GM | Half Bridge (AlN substrate) | 1200 V | 181 A | 8 mΩ | Gen 3 MOS | 150 °C | 62.8 x 56.7 mm | ||||
GM | Half-Bridge | 1200 V | 160 A | 8 mΩ | Gen 3 MOS | 150 °C | 62.8 x 56.7 mm | ||||
GM | Half-Bridge | 1200 V | 160 A | 8 mΩ | Gen 3 MOS | 150 °C | 62.8 x 56.7 mm | ||||
GM | Half Bridge (AlN substrate) | 1200 V | 181 A | 8 mΩ | Gen 3 MOS | 150 °C | 62.8 x 56.7 mm | ||||
FM | Half-Bridge | 1200 V | 117 A | 11 mΩ | Gen 3 MOS | 150 °C | 62.8 x 33.8 mm | ||||
FM | Half-Bridge | 1200 V | 117 A | 11 mΩ | Gen 3 MOS | 150 °C | 62.8 x 33.8 mm | ||||
GM | Half-Bridge | 1200 V | 141 A | 11 mΩ | Gen 3 MOS | 150 °C | 62.8 x 56.7 mm | ||||
GM | Half-Bridge | 1200 V | 141 A | 11 mΩ | Gen 3 MOS | 150 °C | 62.8 x 56.7 mm | ||||
CBB011M12GM4 New | GM | Full-Bridge | 1200 V | 100 A | 11 mΩ | Gen 4 | 175 °C | 62.8 x 56.7 mm | |||
GM | Full-Bridge | 1200 V | 100 A | 11 mΩ | Gen 4 | 175 °C | 62.8 x 56.7 mm | ||||
CHB011M12GM4 New | GM | T-Type | 1200 V | 100 A | 11 mΩ | Gen 4 | 175 °C | 62.8 x 56.7 mm | |||
GM | T-Type | 1200 V | 100 A | 11 mΩ | Gen 4 | 175 °C | 62.8 x 56.7 mm | ||||
FM | Half-Bridge | 1200 V | 84 A | 16 mΩ | Gen 3 MOS | 150 °C | 62.8 x 33.8 mm | ||||
FM | Half-Bridge | 1200 V | 84 A | 16 mΩ | Gen 3 MOS | 150 °C | 62.8 x 33.8 mm | ||||
GM | Six-pack (three-phase) | 1200 V | 50 A | 16 mΩ | Gen 3 MOS | 150 °C | 62.8 x 56.7 mm | ||||
GM | Six-pack (three-phase) | 1200 V | 50 A | 16 mΩ | Gen 3 MOS | 150 °C | 62.8 x 56.7 mm | ||||
FM | Six-pack (three-phase) | 1200 V | 30 A | 21 mΩ | Gen 3 MOS | 150 °C | 62.8 x 33.8 mm | ||||
FM | Full-Bridge | 1200 V | 48 A | 21 mΩ | Gen 3 MOS | 150 °C | 62.8 x 33.8 mm | ||||
FM | Six-pack (three-phase) | 1200 V | 30 A | 21 mΩ | Gen 3 MOS | 150 °C | 62.8 x 33.8 mm | ||||
FM | Full-Bridge | 1200 V | 48 A | 21 mΩ | Gen 3 MOS | 150 °C | 62.8 x 33.8 mm | ||||
FM | Six-pack (three-phase) | 1200 V | 30 A | 32 mΩ | Gen 3 MOS | 150 °C | 62.8 x 33.8 mm | ||||
FM | Full-Bridge | 1200 V | 37 A | 32 mΩ | Gen 3 MOS | 150 °C | 62.8 x 33.8 mm | ||||
FM | Six-pack (three-phase) | 1200 V | 30 A | 32 mΩ | Gen 3 MOS | 150 °C | 62.8 x 33.8 mm | ||||
FM | Full-Bridge | 1200 V | 37 A | 32 mΩ | Gen 3 MOS | 150 °C | 62.8 x 33.8 mm |
End of Section
Featured Design Tools
We lead the pack by making sure silicon carbide system education and design resources are right at your fingertips through our reference designs, evaluation kits, gate drivers, and technical resources. Learn more about Wolfspeed WolfPACK companion parts to better understand how this new module platform can help you increase product performance, accelerate time to market, and lower costs.
Products
Products
Name | Buy Online | Package | Designed By | Product SKU | View Product | Form |
---|---|---|---|---|---|---|
GM | Wolfspeed | KIT-CRD-CIL12N-GMA | Evaluation Tool | |||
FM | Wolfspeed | KIT-CRD-CIL12N-FMA | Evaluation Tool | |||
FM | Wolfspeed | KIT-CRD-CIL12N-FMC | Evaluation Tool | |||
FM, GM, SpeedVal Kit | Wolfspeed | CGD1700HB2M-UNA | Gate Driver Board | |||
FM, GM, SpeedVal Kit | Analog Devices | EVAL-ADUM4146WHB1Z | Gate Driver Board | |||
FM, GM, SpeedVal Kit | Skyworks | Si823H-ACWA-KIT | Gate Driver Board |
End of Section
References
- https://www.wolfspeed.com/knowledge-center/article/demystifying-pcb-layout-methodologies-for-sic-gate-drivers
- https://www.wolfspeed.com/downloads/dl/file/id/1971/product/745/cpwr_an45_wolfspeed_wolfpack_trade_application_note.pdf
- https://www.wolfspeed.com/knowledge-center/article/enabling-system-upgrades-with-sic-technology-using-industry-standard-base-plate-less-packaging
- A. Zeanh et al., “Thermomechanical Modelling and Reliability Study of an IGBT Module for an Aeronautical Application,” EuroSimE 2008 - International Conference on Thermal, Mechanical and Multi-Physics Simulation and Experiments in Microelectronics and Micro-Systems, Freiburg im Breisgau, 2008, pp. 1–7.
- Mauro Ciappa, “Selected failure mechanisms of modern power modules,” Microelectronics Reliability, Volume 42, Issues 4–5, 2002, pp. 653–667, ISSN 0026-2714, https://doi.org/10.1016/S0026-2714(02)00042-2.