Practical Tools for Designing with Silicon Carbide in Industrial Motor Drives
Article
Industrial electric motors, including industrial low voltage motor drives, servo drives, heat pumps and air conditioners, together account for more than 45% of all global electricity consumed annually.
As the demand for energy grows, more stringent efficiency standards, or minimum energy performance standards (MEPS), are emerging to reduce the environmental impact that industrial motor drives have on the warming planet. To-date, more than 50 countries worldwide, including the EU, China and the USA, have regulations in place governing the efficiency of industrial low voltage motor drives. Present day industrial motor designs are driven primarily by the global efficiency standard IEC 60034-1-30 that outlines levels IE1 through IE4. Recently an additional IE5, or ultra-premium efficiency, standard was added. These IE norms apply to all motor systems that are supplied using the power grid. To-date, most countries already require a minimum IE3 standard.
In the EU, motors are now required to meet the IE4 regulation. In traditional drives IE4 only applies to the motor and not the drive. However, in the case of embedded drives where the motor and drive are integrated into one compact unit the entire system is required to meet IE4.
Using silicon carbide in place of traditional silicon-based IGBTs in the drive circuit enables system designers to reach the most stringent IE4 efficiency standards while designing smaller, lighter embedded motor drive systems. This article walks through how to simplify, accelerate and derisk the silicon carbide design process, and more easily access IE4 and IE5 energy savings in industrial motor drive systems.
Simplify, accelerate and derisk the design process when designing industrial motor drives with silicon carbide and easily access IE4 and IE5 efficiency standards.
Step 1: Learn
Whether you have experience with silicon carbide components, or are new to the technology, the first stage in the design process is becoming familiar with the range of silicon carbide products and learning the key differentiators between them. These differences can include package size, voltage class, switching speed and efficiency.
Simulators provide a quick and reliable way to explore system needs and how SiC devices will perform within them and provide an ideal platform for designers to model systems, determine the correct voltage class or power need for an application and aide in selecting the most applicable devices for further testing.
Wolfspeed’s SpeedFit™ Design Simulator is an online PLECS-based simulation tool that offers an easy-to-use interface for evaluating silicon carbide MOSFETs, diodes and power modules.
SpeedFit offers more than 35 topologies, including several three-phase inverter topologies. To get started, specify basic operating points for the desired application and choose from a recommended list of silicon carbide products. Then, input detailed circuit parameters, operating conditions, and thermal parameters dependent on the topology. Transient operating points may be enabled to see the effect of overload conditions on the thermal performance. SpeedFit offers flexibility in the thermal system configuration, allowing thermal parameters to be inserted as a fixed heatsink temperature, or as a thermal impedance to ambient. If the end thermal system is unknown, this step can be used to determine the thermal requirements of the system.
An example of desired parameters for an 11 kW motor drive for a heat pump application and the SpeedFit simulator input can be seen in Figure 1.
Parameter | Specification |
---|---|
Input Voltage | 550 - 850 VDC |
Motor Voltage | 380 - 480 VAC |
Inverter Efficiency | >98% for 20 - 100% loading |
Switching Frequency | >15 kHz |
Maximum dv/dt | 20 V/ns |
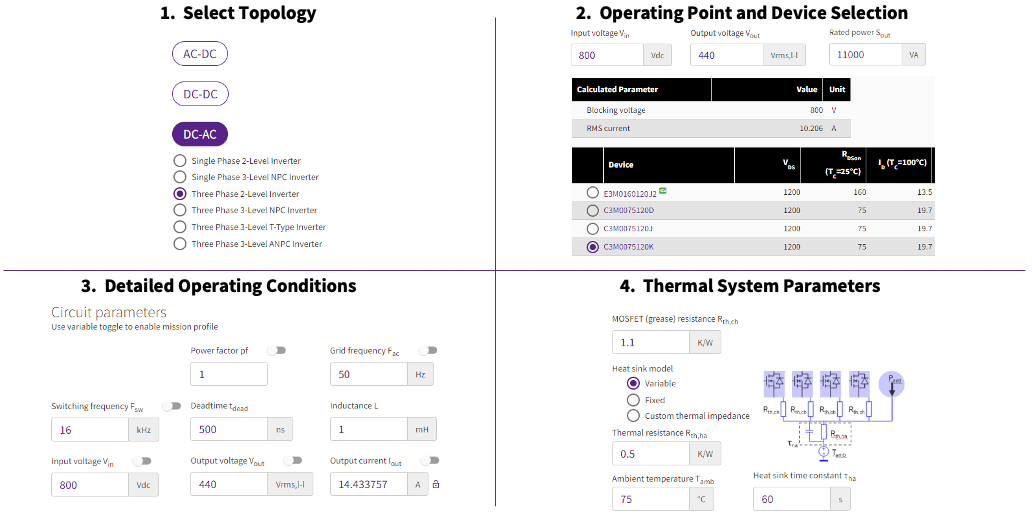
Once parameters are entered, the simulation can be run to determine results within seconds. Results include waveforms to determine how the converter is operating, junction temperature, power loss and efficiency. From here, the result can be held while adjusting previous inputs. This allows easy comparison between the performance of different parts under different operating conditions and identifies the best MOSFETs or power modules for the system requirements. Save simulation results as a PDF or CSV, or request samples directly to begin the evaluation stage.
Additional PLECS and LTspice models for all devices are provided for designers who wish to perform more in-depth system or circuit simulation offline.
Step 2: Evaluate
Further hone industrial motor drive designs by evaluating which SiC device best fits the desired application. Evaluation is a crucial step in determining and comparing efficiencies between silicon carbide and traditional IGBTs. Traditional hands-on testing methods can take weeks, significantly slowing the design process while manipulating system parameters and optimizing the overall system.
Using evaluation kits, designers can evaluate device and system performance and receive results in minutes, making the design process faster and more efficient.
Evaluation kits like the SpeedVal™ Kit Modular Evaluation Platform allow rapid testing of specific silicon carbide discrete devices in three-phase motor drive systems. The SpeedVal Kit, which was created specifically for three-phase motor drive applications, offers a modular set of building blocks that can be easily swapped for rapid in-circuit evaluation of system performance at real operating points.
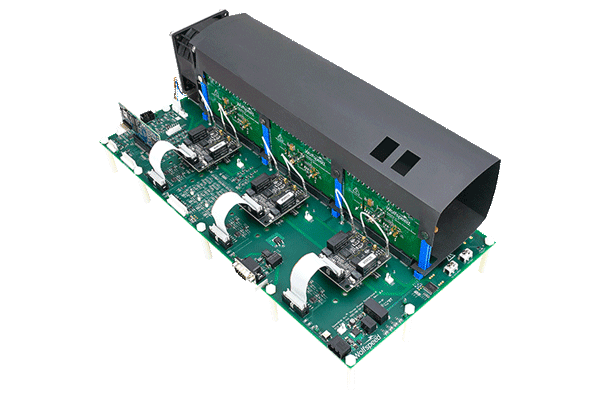
Use SpeedVal Kit to evaluate and optimize the high-speed dynamic switching performance of Wolfspeed’s 650 V to 1200 V SiC MOSFETs paired with your choice of gate drivers from industry-leading partners. The three-phase motherboard includes open loop firmware for testing devices on static loads and provides a platform for advanced control and firmware development for motor control. Also included are hardware interfaces for both encoders and resolvers to support closed loop speed and position control.
SpeedVal Kit also allows for dynamic testing, including double-pulse and short-circuit tests. These platforms are built to have optimized test points to allow high-fidelity current and voltage readings. With these readings in mind designers then tune the dV/dt, a critical parameter in motor drive applications to ensure compatibility with existing motors and adjust gate resistance and gate capacitance to tune switching behavior. Together, optimized dV/dt and gate resistance further solidifies the powertrain design and streamlines the final development stage.
Step 3: Develop
During the final development stage designers apply knowledge gleaned from learning and evaluation to confidently build an optimized silicon carbide system. Reference designs aid in the development stage and provide examples of proven schematics and layouts of power systems. These designs fit a range of applications, can be scaled depending on the power level of the system and can be adjusted to meet cost requirements.
Two new Wolfspeed reference designs are optimized for designing motor drives with silicon carbide: the 25 kW FM3 Three-Phase Inverter and the 11 kW High-Efficiency Three-Phase Motor Drive Inverter.
The 25 kW FM3 Three-Phase Inverter offers a comprehensive design package supporting early SiC design-in activities, enabling engineers to quickly evaluate performance out of the box as a simple three-phase inverter topology. It utilizes a single Wolfspeed WolfPACK™ FM3 power module to achieve peak efficiencies over 99.5% and power density of 5.7 kW/L. This comprehensive design package offers customizable firmware, isolated CAN communication and GUI, and adaptable power stages to maximize operating condition flexibility.
The 11 kW High Efficiency Three-Phase Motor Drive Inverter demonstrates Wolfspeed’s 1200 V MOSFETs in industrial heating and cooling applications and achieves peak efficiencies of 99% and full load efficiency of 98.6%. This represents a 1.5% efficiency improvement over a comparable IGBT solution at 16kHz.
Conclusion
Using support tools can make the silicon carbide design process more approachable and efficient, lowering the barrier to entry when transitioning from silicon to silicon carbide for industrial motor drives. Through the three-stage design process engineers can revolutionize industrial motor drive systems and meet leading IE4 and IE5 efficiency standards. Still have questions? Connect directly with silicon carbide application engineers at the Wolfspeed Power Applications Forum to access our knowledge base, ask technical questions in a community forum or reach us through private chat. To get started designing with Wolfspeed silicon carbide, visit: https://www.wolfspeed.com/tools-and-support.