Silicon Carbide Meets Power V2G Demands in EV Fast-Charger Market
Article
Abstract
The recent bounce back in the automotive industry, a vigorous resurgence in consumer interest for green technologies, and increasing regulatory support has driven up electric vehicle (EV) market expectations.
EVs have come close to addressing “range anxiety” among customers who are used to the 400-mile range possible by vehicles using internal combustion engines. The latest EVs deliver close to a 200-mile range, with 300 miles expected to soon become commonplace. At the leading edge, the base Tesla S model offers just over 400 miles, and a new luxury EV trendsetter, Lucid Motors, has crossed that mark with models delivering over 500 miles.
This paper explores how silicon carbide (SiC) technology continues to be a leading solution for power and vehicle-to-grid (V2G) demands in the fast growing fast-charger market.
The road to 15-minute charging solutions
Sustaining EV growth requires an infrastructure of chargers that cuts charging times down to 12–15 minutes for 80% capacity. Increasing the voltage can safely achieve higher power delivery required by such fast chargers. The high voltage allows lower current, which, in turn, reduces power loss in the cables as well as battery overheating to allow better power retention. It also allows for weight reduction, as less copper is needed by reduced cable size, which frees up space and weight. Smaller cable dimensions also helps to lower the cost of expensive copper cables and connectors.
Tesla started that trend with the 400-V “Supercharger” network, but it is not quite enough to achieve the 15-minute goal. A key trend, therefore, is toward an 800-V architecture (Figure 1).
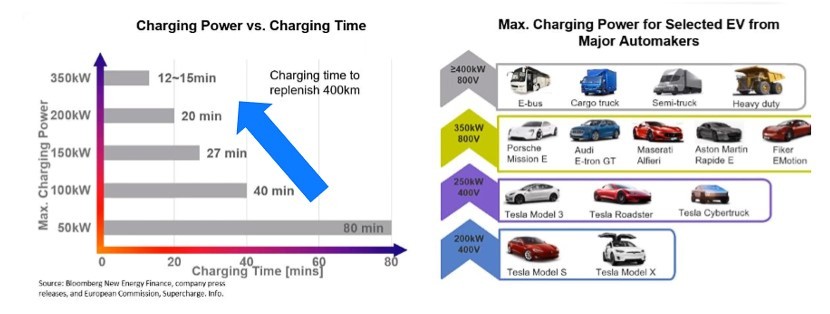
Several new models, like Porsche’s Taycon, Hyundai’s Kia EV6, and General Motors’ Hummer EV, already use 800-V DC fast charging. Lucid has even gone beyond that level with its 900-V architecture.
This has required EV companies to make substantial modifications to every device — from increasing turns in motor winding and strengthening insulation for conductors to redesigning the power stage to use leading-edge components with blocking voltages higher than 800 V.
Bidirectionality for V2G
Yet another important trend that chargers must support is vehicle-to-grid (V2G). V2G is gradually developing as companies innovate compelling business models for powerful energy storage systems (ESS) on wheels. While solar power and stationary ESS will certainly have an important place in the electrified future, V2G is being looked at for dealing with load peaks.
Consider large commercial/industrial energy consumers who must pay a penalty both for peak power demanded as well as high average power factor. A bidirectional DC fast charger that can switch from charging employee EVs to feeding the enterprise premises or grid during peak loads makes a compelling economic case for installation.
Fermata Energy, for instance, is testing devices in Ahoskie, North Carolina, that will eventually help integrate EVs with buildings and the grid. Its aim is to turn EVs into valuable ESS assets that not only increase energy resilience and reduce energy costs but eventually deliver services like frequency regulation.
On a smaller scale, these ESS assets can provide consumers with backup during power outages and offer campers and commercial contractors, including those supporting remote TV/movie shoots, with portable power or provide temporary power in the event of a utility outage. On a larger scale, V2G can tie into the national power grid to smoothe fluctuations in renewable sources like wind and solar.
SiC enables 800-V architecture
Silicon carbide (SiC) is the key technology making the move to high-voltage fast chargers possible. SiC devices offer several advantages over silicon (Si) counterparts:
- A 10× higher breakdown field enables high blocking voltages in smaller die area than silicon. (SiC today supports MOSFET blocking up to 1700 V whereas a silicon super junction MOSFET is generally limited to below 900 V.)
- Lower on-state resistance and lower off-state leakage currents than Si contribute to higher efficiency.
- Very low or no reverse recovery current and the ability to switch at 3× to 5× higher system frequencies than Si reducing the size and weight of capacitors and magnetics.
- A 3× higher thermal conductivity and the ability to withstand higher chip temperatures reduce cooling requirements.
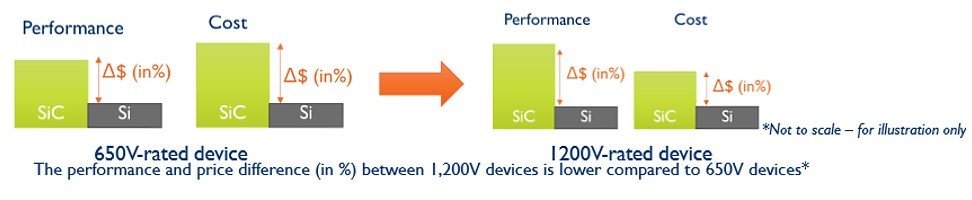
These characteristics place 1,200-V SiC devices in a significantly advantageous cost/performance position (Figure 2) over Si insulated-gate bipolar transistors (IGBTs), offering the higher efficiencies, thermal profiles, and power densities needed to enable the 800- to 900-V EV architectures. No wonder then, that Yole Développement expects SiC in off-board chargers to grow from about $10 million today to nearly $225 million in 2025.
Stacked for power
Both on-board and off-board EV fast chargers comprise two main blocks: an active front end (AFE) for AC/DC conversion and a DC/DC converter. The AFE gets single-phase or three-phase power from the grid and outputs to DC intermediate voltages, which are then converted by the DC/DC block to the voltage required for fast-charging the EV batteries.
Whereas OBCs typically use a single 3- to 11-kW module, off-board chargers have 15kW–30kW modules stacked to reach 150 kW today and up to the more recent goal of 350 kW. The latest SiC devices, packages, and circuit topologies make it possible to achieve this with fewer 60-kW blocks in the near future.
The key component
Wolfspeed offers the key component to support these trends in the EV market — a broad portfolio of 1,200-V MOSFETs and Schottky diodes. The company’s 1,200-V blocking-voltage third-generation (C3M) MOSFET lineup includes models with current ratings ranging from 7.2 A to 115 A, on-resistances (RDS(ON)) from 350 mΩ to 16 mΩ, and maximum junction temperatures of 150°C or 175°C.
The devices are offered in standard TO-247-3 as well as optimized/enhanced TO-247-4 and TO263-7 packages with Kelvin source pin connections to aid in optimizing performance from these ultra-fast SiC devices.
References for new designs
Wolfspeed also offers reference designs that ease design effort and shorten times to market. To address the latest EV charger trends, the company has developed a 22-kW solution, which comprises an AFE and a flexible DC/DC converter, for either OBCs or as a power block in DC fast chargers (Figure 4).
Description | 3phase AC input Charging | 1phase AC input Charging | Discharging Mode |
---|---|---|---|
Input Voltage | 304Vac~456Vac | 90Vac~277Vac | 300Vdc-800Vdc |
Output Voltage | 200-800Vdc | 200-800Vdc | 220Vac |
Rated Power | 22kW 36A max | 6.6kW | 6.6kW |
OBC peak Efficiency | >96% | >96% | >96% |
DCDC peak Efficiency | >98.5% | >98.5% | >98.5% |
DC Bus Voltage | 650V-900V | 380V-900V | 360V-760V |
The combination of two reference boards is unique in its ability to support bidirectional single- and three-phase operation and meet the needs of a fixed battery voltage in an OBC as well as a variable 200–800 V for DC fast chargers that must serve both the older and the 800-V EVs. The flexibility of the AFE and DC/DC designs opens up opportunities for engineers targeting applications beyond EVs, such as ESS, UPS, and other industrial power-conversion systems.
1,200-V SiC increases performance, simplifies design
A simple six-switch topology is used for the CRD-22AD12N AFE (Figure 5, right) operating at 45 kHz. Although the switches support much higher frequencies, there are tradeoffs to be considered between inductive core losses and switch efficiencies. This topology directly replaces the similar six-IGBT circuit, which, while simple and inexpensive but, exhibits poor efficiency, high switching losses, and — due to the IGBT tail current — a much lower frequency of less than 20 kHz.
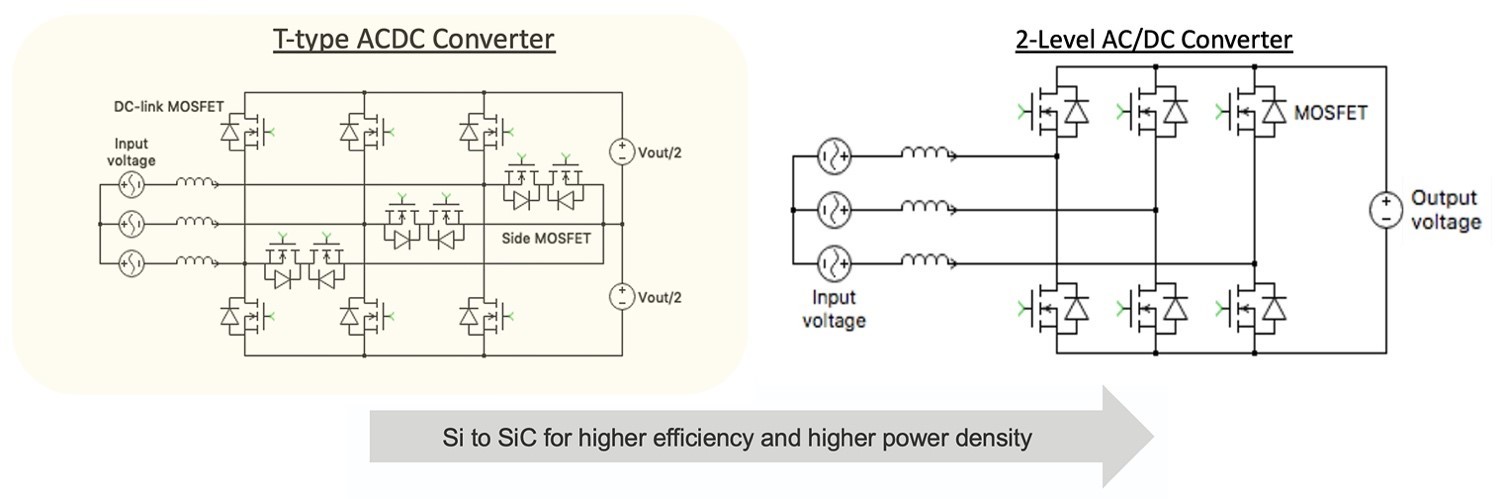
To achieve the benefits of high switching frequency, a T-type AFE topology may be implemented when adding additional 650V silicon or SiC devices, but it is worth noting that this comes with significant tradeoffs, including a higher part count, complex control, and higher system cost.
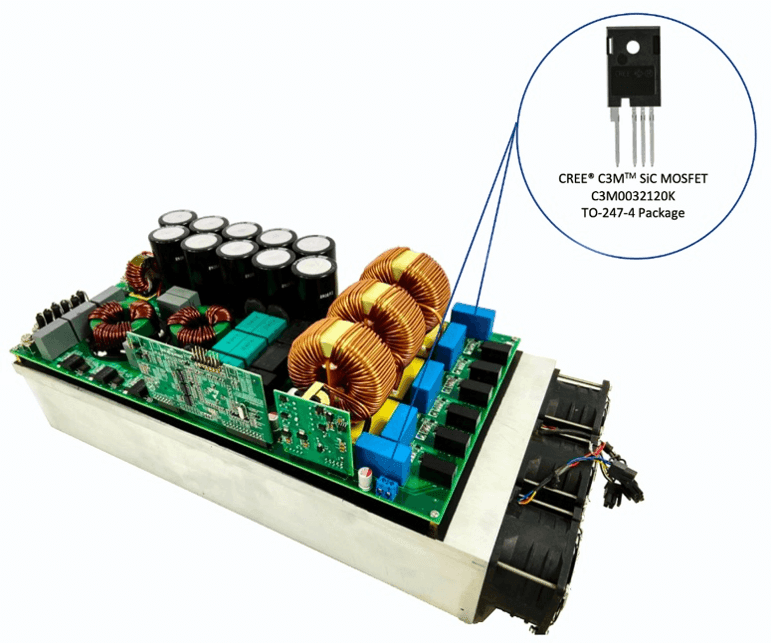
The CRD-22AD12N uses the 1,200-V, 32-mΩ C3M0032120K SiC MOSFETs in TO-247-4 packages and the powder core KAM-material–based PFC choke that offers a good combination between the relatively low power loss density (Pv) of 200 kW/m3, and an excellent DC bias of 68%, as well as a high-frequency range of up to 300 kHz.
The C3M MOSFETs and a flexible control scheme allow the board to surpass Si performance, offering the following:
- High power density of 4.6 kW/L
- High efficiency of >98.5% in charging and discharging mode
- Bidirectional operation
- Support the DC link from both three-phase AC and single-phase AC inputs
- Support 200- to 800-VDC battery voltage range for compatibility with older and future EV architectures
In single-phase application, the AFE evaluation board outputs 6.6 kW; for three-phase, 22 kW.
For the DC/DC section of the charger to achieve the required performance levels, it is necessary to use complex, multi-level topologies with 650-V Si or SiC devices, such as the cascade converter shown in Figure 7. The Si 650-V device solution would offer an 80- to 120-kHz switching frequency range, requiring higher switch and driver counts, higher system costs, and complex current-sharing control while also suffering from higher conduction losses.
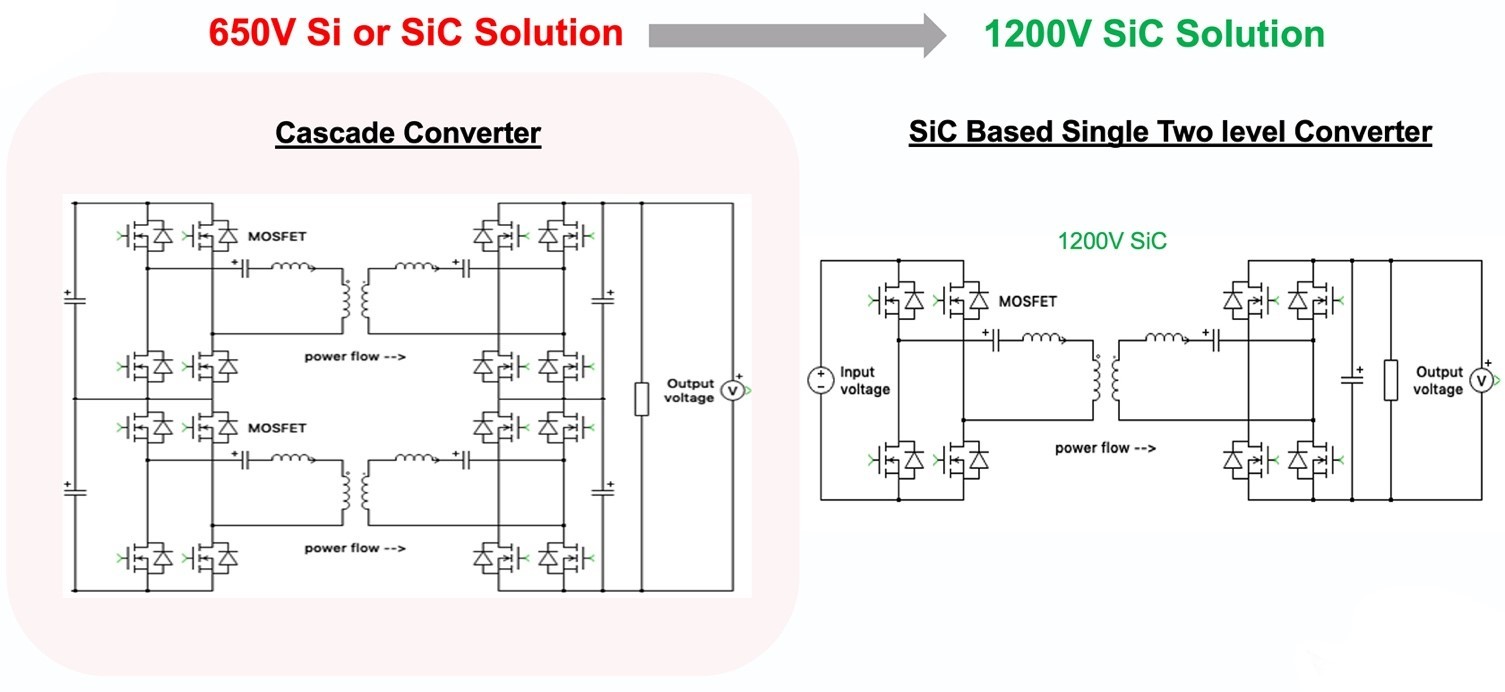
With the C3M0032120K part used instead, Wolfspeed could achieve better performance and a switching frequency range of 140–250 kHz that contributes to smaller, lighter magnetics.
The CRD-22DD12N DC/DC board is a full-bridge CLLC resonant converter with a flexible control scheme that implements frequency modulation, phase-shift control, adaptive synchronous rectification, and a bridge reconfiguration technique. Its topology allows for zero-voltage turn-on, low-current turn-off for lower switching losses, and lower EMI. All of that is accomplished along with a lower part count and lower system cost.
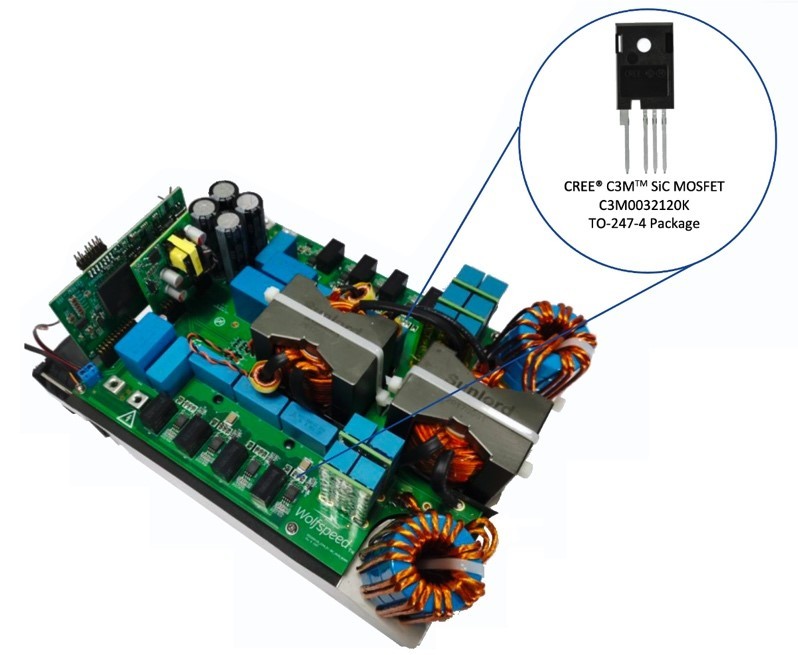
It is compatible with a DC bus input voltage range of 380–900 V and a DC output voltage range of 200–800 V, allowing it to be integrated with both single-phase and three-phase AFEs.
Like the AFE, this board offers a high-power density of 8 kW/L and high efficiency of >98.5% in charging and discharging mode.
Aggregating SiC advantages
Combining the AFE and DC/DC boards result in significant advantages over Si-based implementations (Figure 9).
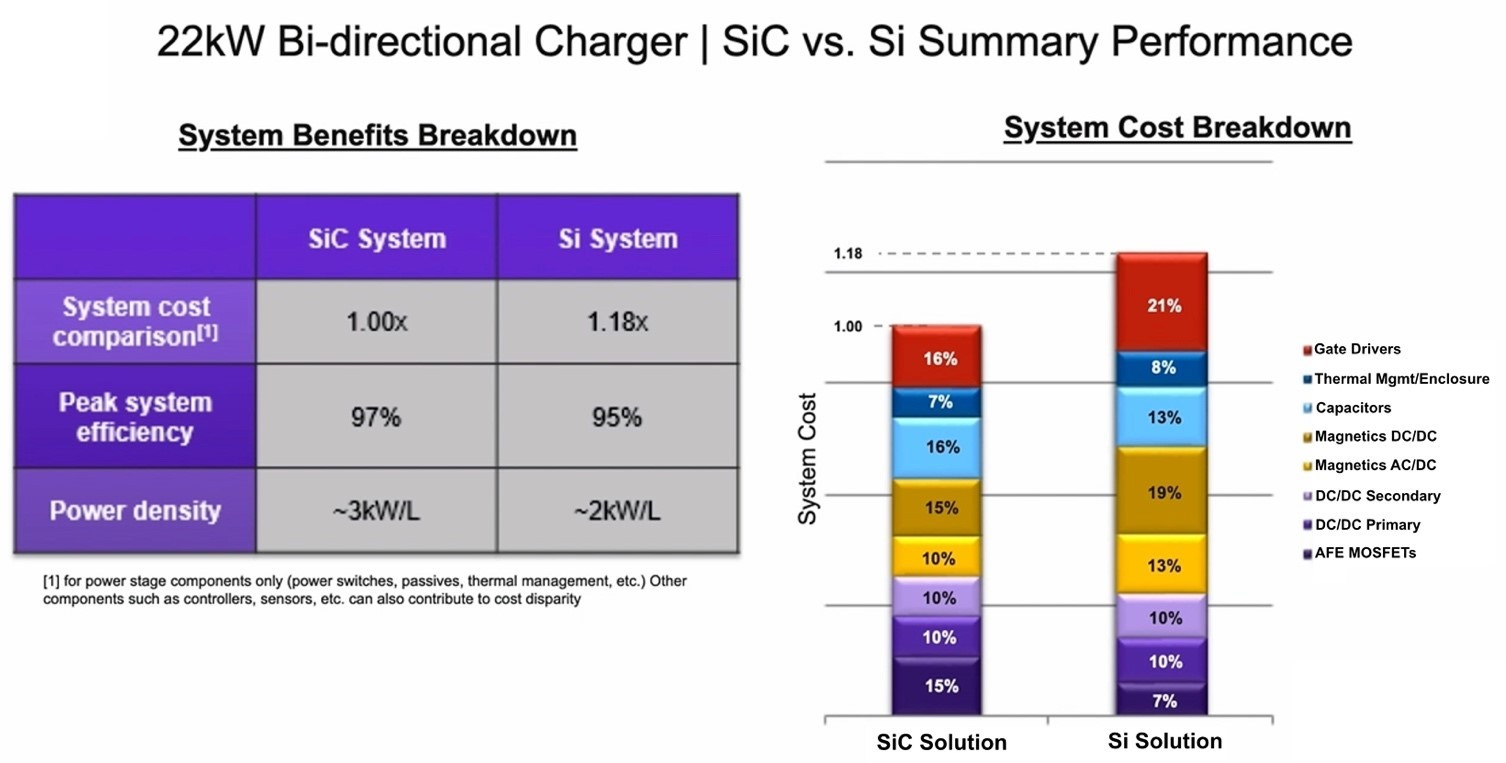
Conclusions
As EV battery voltages move toward 800 V, 1,200-V SiC switches are not only enabling the new EV architecture that aims to achieve 15-minute charging but opening up new opportunities in V2G applications with bidirectional chargers.
Wolfspeed’s work in designing the CRD-22AD12N AFE with the CRD-22DD12N DC/DC reference boards for engineers shows that the use of SiC devices more than makes up for the premium over Si device costs by reducing overall system costs, cutting down on weight and size, increasing system efficiency, easing thermal design and cost burden, and potentially shortening time to market by simplifying power system design.
Visit Wolfspeed’s automotive technology page to learn more.