The Batteries that Power EVs
Article
The battery pack accounts for 35% to 50% of a battery EV’s (BEV’s) cost1 and is similarly a significant contributor to size and weight along with 100% of its range. A keen focus on battery prices and technology by EV makers as well as battery makers should therefore come as no surprise.
Consider this: Bloomberg New Energy Finance’s (BNEF’s) 2021 Battery Price Survey predicts that by 2024, the average pack prices could go below $100/kWh. That is the price point at which automakers could manufacture and sell mass-market EVs at the same price and margin as comparable internal combustion vehicles and without subsidies.2
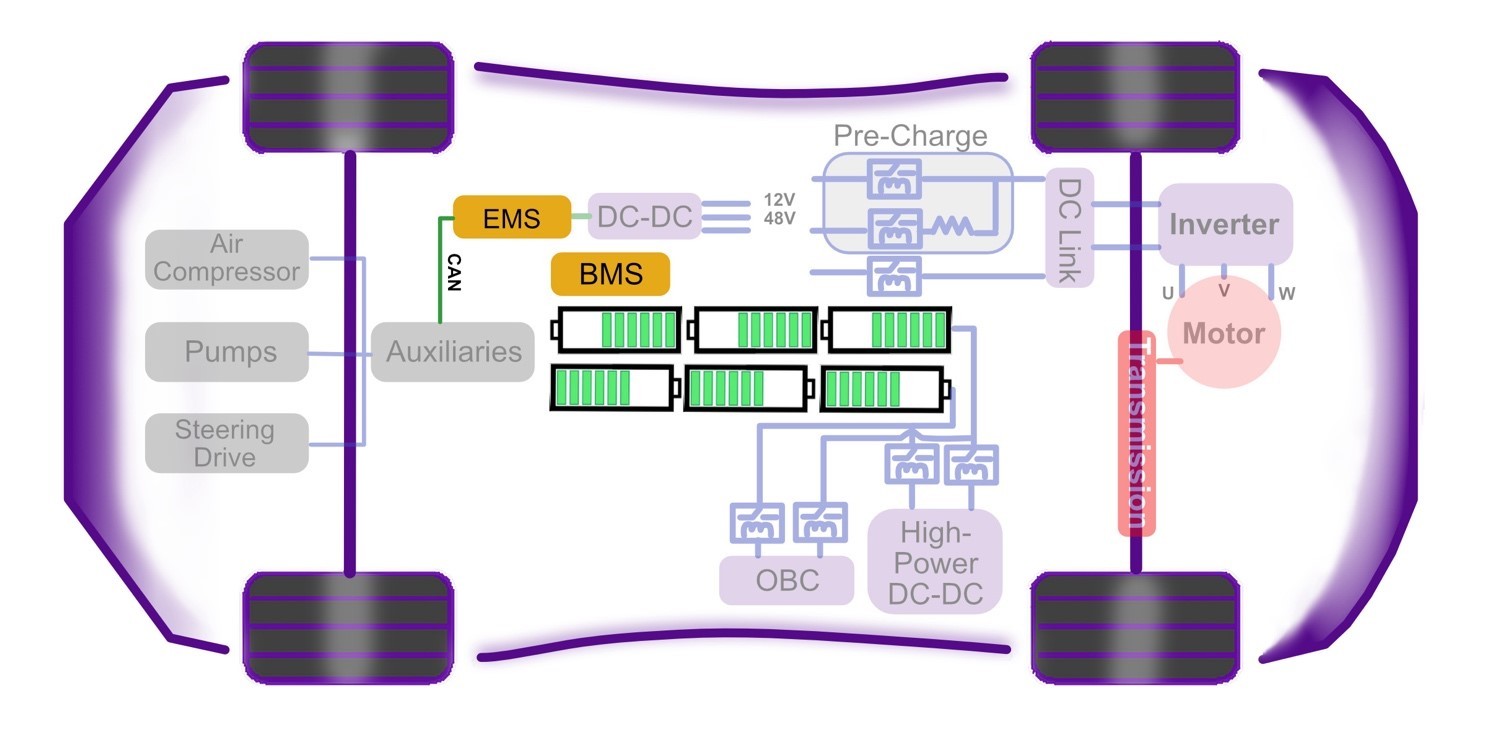
This chapter of Wolfspeed’s What’s Under the Hood series shines the light under the hood on the powerhouse of BEVs — the battery pack (Figure 1) — to reveal cell characteristics, battery chemistries, and architectures, as well as hazards, protections, and control.
Batteries as electrochemical factories
Rechargeable or “secondary” batteries convert chemical energy into electrical energy and vice versa. Cells (Figure 2) are the smallest individual electrochemical units within modules and packs.3
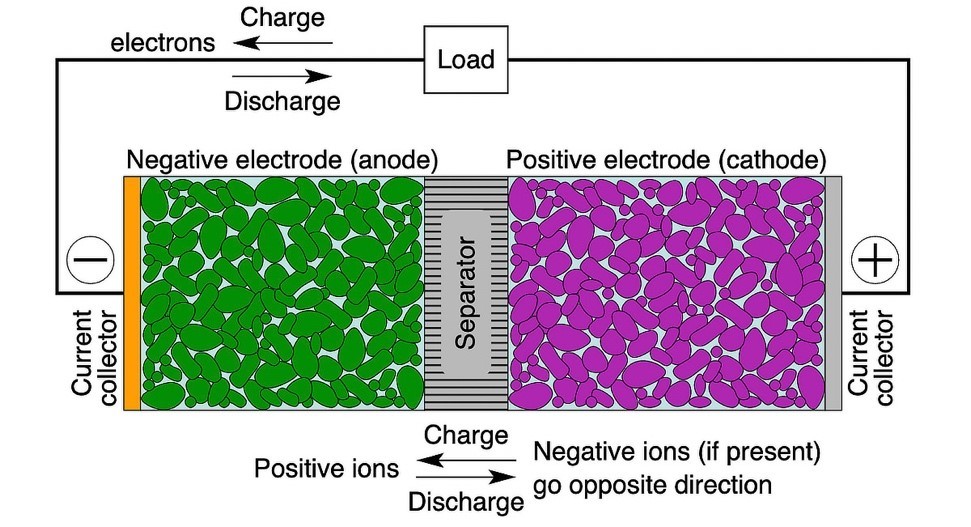
Industry names of battery chemistries generally refer to the electrode material. In a Li-ion battery, for instance, the cathode generally comprises lithium metal oxide particles and anode graphite particles. Both are physically separated by a membrane to prevent an internal short but are permeated with an electrolyte to aid movement of Li+ ions. During discharge, electrons travel from the negative electrode to the positive electrode external to the battery through the load, while Li+ ions travel in the reverse direction inside the cell. During charging, the direction of electron and ion flows is reversed.
Key battery specs
Each cell is characterized by a number of parameters that are largely dependent on battery chemistry and packaging. They enable comparison of various battery packs and include:
- Nominal voltage (V): The reference or “normal” voltage of the battery.
- Nominal capacity (Ah @ specified C-rate): It is the coulometric capacity measured in ampere-hours delivered when a fully charged battery is discharged at a certain discharge current (specified by the C-rate).
- C-rate: This measures the rate at which a battery is discharged relative to its maximum capacity. A 1C rate means that the discharge current will discharge the entire battery in one hour. Higher-voltage battery packs allow lower C-rate cells and faster charging and discharging by requiring lower current.
- Specific energy (Wh/kg): This is nominal battery energy per unit mass or the gravimetric energy density, which reflects on the driving range.
- Specific power (W/kg): The maximum available power per unit mass demonstrates the ability to deliver high current on demand that affects vehicle acceleration.
- Energy density (Wh/L): The nominal battery energy per unit volume or volumetric energy density. It determines the battery size required to achieve a given range for a given energy consumption.
- Performance: Typically, energy or power versus cycle lifetime, performance reflects the condition of the battery, especially when driving an EV in extreme temperature conditions.
- Lifespan: This is measured in charge-discharge cycle count. A Li-ion EV battery pack life is generally expected to be 10–12 years.
Cost is another parameter used to judge viability of battery technology. It not only includes technology, material, and manufacturing cost but also cost of secondary systems such as those for safety and battery monitoring and management.
EV battery chemistries
As mentioned above, battery chemistry drives the parameters that matter to EV applications. The nickel-cadmium (Ni-Cd) batteries utilized by early EVs have given away to newer battery chemistries. Although stable over a wide temperature range, Ni-Cd is beset by a number of issues, including a low nominal voltage of 1.2 V, low energy density, and a voltage-suppression problem known as “memory effect” that results in lower capacity when the battery does not complete charge-discharge cycles.
Among the more mainstream technologies are the Li-ion chemistries described below and compared in Figure 3.4
- LCO: Lithium cobalt oxide (LiCoO2) offers high gravimetric energy density and a 3.6-V nominal voltage but has a low C-rate, short lifespan, stability issues over temperature, and high cost from cobalt use.
- Nickel-based chemistries: Although both nickel and cobalt significantly increase battery cost, lithium nickel manganese cobalt oxide (NMC) and lithium nickel cobalt aluminum oxide (NCA) are used heavily in EV traction as well as storage applications due to their high specific energy and a good nominal voltage of 3.6 V. NMC takes the lion’s share, with 71% of sales, with much of the rest taken up by NCA.1 However, the industry is increasingly concerned about cobalt beyond its high cost — its supply chains is often tainted by difficult-to-track and questionable to illegal mining practices.
- LMO: Lithium manganese oxide offers both high C-rates and high nominal voltage (3.7 V) and has been used in older EVs. However, performance is lower than other chemistries.
- LFP: Lithium iron phosphate (LiFePO4) is stable across a wide temperature range and is therefore safer. It has a longer lifespan and high C-rates but relatively lower capacity and a lower nominal voltage of 3.2 V. LFP cells were also almost 30% cheaper than NMC cells in 2021.3 Since LFP cathode composition is close to that of the phosphates used as food additives with similar purity level requirements, it can leverage a well-established manufacturing environment practice and controls. Moreover, LFP does not have the supply chain issues associated with cobalt. EV makers are therefore increasingly turning to LFP battery technology, particularly for the more economical models.
- LTO: In these batteries, the negative electrode is a spinel-structured lithium titanate (Li4Ti5O12) instead of graphite. The positive electrode can be LMO or NMC. LTO batteries are much safer, have a longer lifespan, offer better performance, and have a lower cost. However, their specific energy is low. LTO batteries are used in Honda’s Fit EV and some Japan-only versions of Mitsubishi’s i-MiEV.4
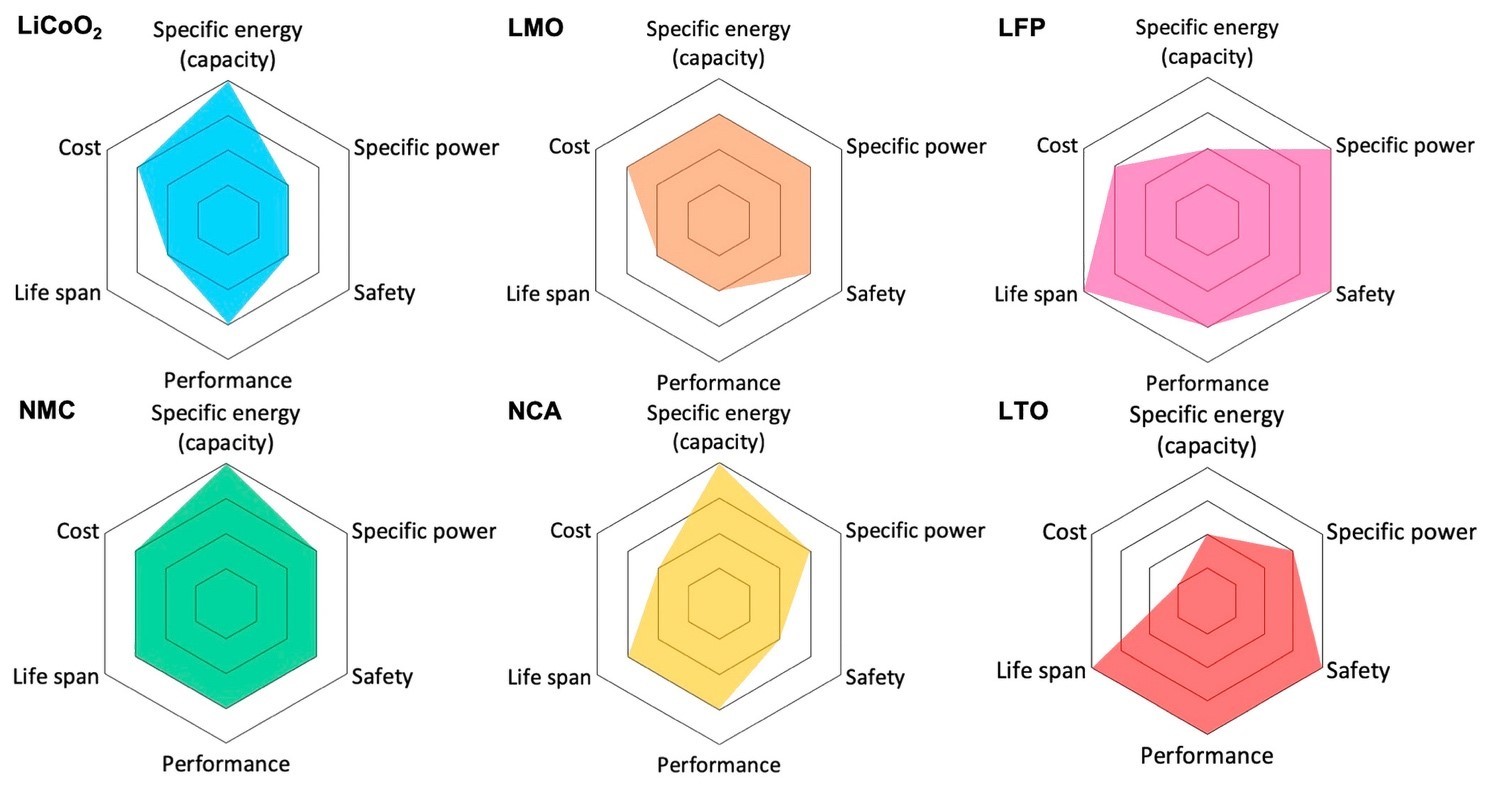
Cell form factors & pack anatomy
Cells are packaged as cylindrical, pouch, and prismatic types. A cylindrical cell comprises sheet-like electrodes and separators sandwiched, rolled up, and packed into cylindrical cans. The 18650 (18 × 650 mm) is a popular format that is used by Tesla, and other common sizes include 21700 and 46800. They are well suited to running heat exchangers in the space between them in modules and packs.
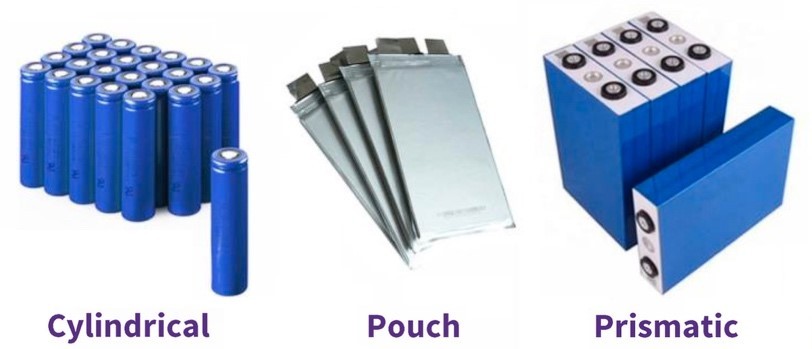
Pouch cells have the electrodes and separator tightly stacked inside a sealed flexible foil container. They require a support structure and face thermal management and cell-swelling issues.
To achieve the prismatic format, sheets of electrodes and separator are sandwiched and either stacked or rolled up and press-fit into metal or hard-plastic housing. They offer high power and high current and are the most commonly used in EVs.
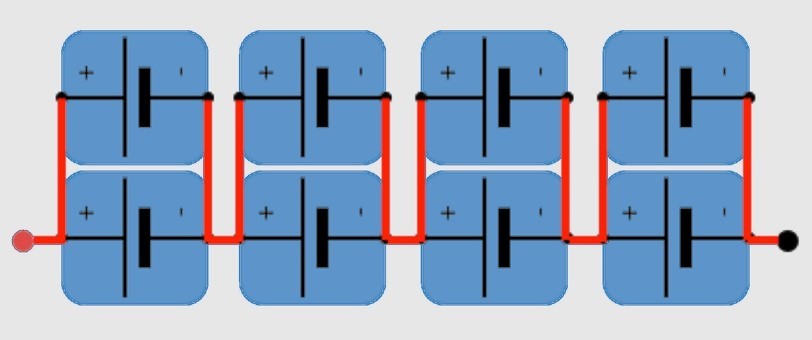
To form batteries, cells are arranged in parallel (P) and series (S), depending on voltage and current requirements. For instance, a 2P4S configuration has two cells in parallel for twice the current and four in series for 4X the voltage (Figure 5). Bus bars are used to connect cell modules to form the entire vehicle battery pack.
EV battery packs range from a few kilowatt-hours for hybrids to over 100 kWh for BEVs. The 400-V systems typically have 96–108 cells in series for 355- to 400-V nominal voltage and 454-V charging, whereas 800-V systems require about 198 cells in series to reach 733-V nominal voltage with 832-V charging.
Li-ion cell hazards & concerns
Li-ion batteries were developed to address the inherent instability of lithium metal batteries. Li-ion cells are safe if certain precautions are taken. However, it is important to understand what can go wrong:
- Dendritic growth: The main cause of internal short-circuits is lithium dendrite formation due to overcharging, discharging below a certain threshold, or charging at a lower-than-recommended temperature. Lithium dendrites grow due to electrodeposition (plating) on the negative electrode and eventually puncture the separator membrane to reach the positive electrode. This can cause excessive heat generation, combustion, and even explosion.
- Thermal runaway: Heating effects from internal self-discharge and internal resistance drive chemical reactions that further heat the battery. This vicious circle continues until the battery catches fire. Thermal runaway in a single cell can cause a chain reaction in the whole pack. Rapid discharging, overcharging, and current surges can cause a thermal runaway event.
- Corrosion, crystal formation, and passivation: Corrosion, the result of undesired oxidation of lithium, leads to increase in internal impedance. Particles on electrodes may develop large crystals, reducing the surface area that the lithium can bind to for normal electrochemical reactions. And a thin passivation layer may grow on the surface of electrodes, typically oxides or oxyhydroxides. These defects all impede desired electrochemical reactions, increase the cell’s internal resistance, and reduce capacity.
Other issues with Li-ion include cell cracking and outgassing. Like dendritic growths, these problems can cause catastrophic failure that may result in fire or hazardous electrolyte spillage.
Battery protection and control
Operated under optimum conditions, electrochemical cells can continue functioning for a long time. For instance, the Oxford Electric Bell comprised of two brass bells, each positioned beneath a dry battery, has been chiming continuously at 2 Hz since it was setup in 1840 — for over 180 years.5
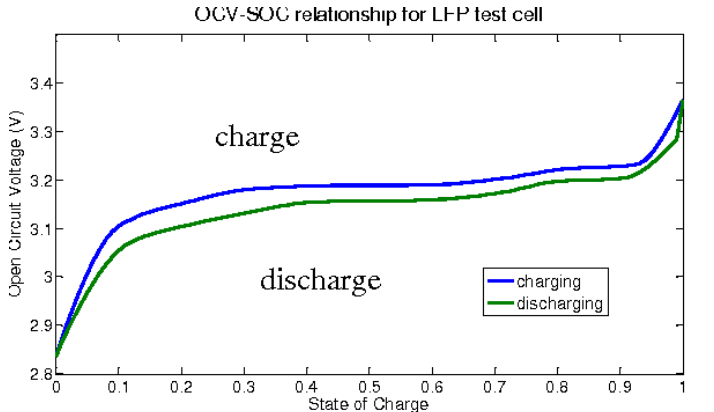
For Li-ion, unique cell characteristics must be considered when monitoring battery conditions to ensure longevity. Its discharge voltage versus state of charge (SOC) is nearly flat between 20% and 80% charge, making it difficult to gauge SOC. Compounding this problem, the Li-ion charge-discharge cycle exhibits “hysteresis” following slightly different voltage versus SOC curves (Figure 6).
Cell monitoring is essential for battery protection. The following conditions are monitored, and if a fault condition is detected, protection measures, like disengaging contractors to open the circuit, are taken.
- Cell balancing: While cells are matched during manufacturing, variation in capacity and internal resistance is a natural outcome of charge-discharge cycles. When multiple cells are stacked in series, the weakest cell limits the current drawn from the stack. Cells are balanced by bypassing strong or weak cells during charging and discharging cycles (Figure 7).
- Overcurrent: This condition must be ascertained to trip contactors and protect the cell from overheating.
- Voltage: Overvoltage and undervoltage conditions are measured at the cell level as well as battery pack level to ensure longevity.
- Cable insulation: The cable insulation resistance is measured by passing a very low current so that insulation breaks can be detected.
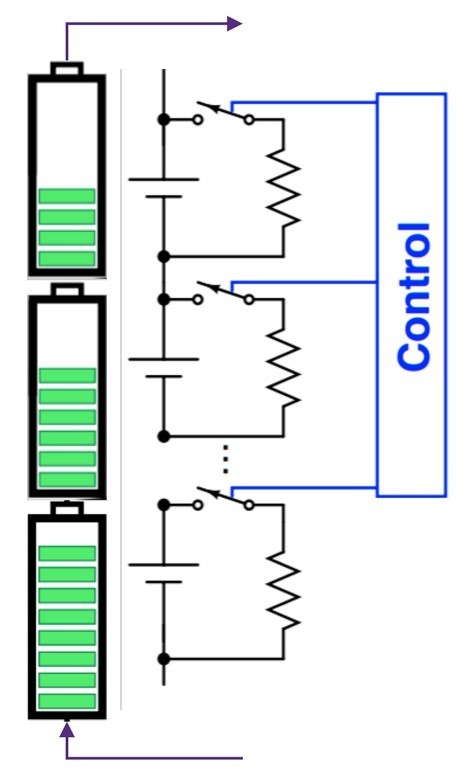
The cell control methods are usually implemented over the wired CAN bus such that each module talks to a central microcontroller unit, which in turn processes the monitoring information and initiates protection measures such as engaging or disengaging contactors.
Conclusion
Given its importance to the BEV market growth, significant R&D is focused on bringing about new battery technologies. A silicon-carbon anode material from Group14 Technologies, for example, is claimed to increase gravimetric energy density by nearly 25% to 330 Wh/kg.6 Other research into solid-state batteries could eliminate fire risk.
To further your knowledge of the EV powertrain with tutorials such as this one, visit the Power Products Knowledge Center.
References
- McKinsey & Co. “Building better batteries: Insights on chemistry and design from China.” April 2021. https://www.mckinsey.com/industries/automotive-and-assembly/our-insights/building-better-batteries-insights-on-chemistry-and-design-from-china
- BNEF. “Battery Pack Prices Fall to an Average of $132/kWh, But Rising Commodity Prices Start to Bite.” Nov. 2021. https://about.bnef.com/blog/battery-pack-prices-fall-to-an-average-of-132-kwh-but-rising-commodity-prices-start-to-bite/
- Dr. Gregory L. Plett, Battery Bootcamp, University of Colorado, Colorado Springs. http://mocha-java.uccs.edu/ECE5710/ECE5710-Notes01.pdf
- Miao et al. “Current Li-Ion Battery Technologies in Electric Vehicles and Opportunities for Advancements.” MDPI, 2019. https://www.mdpi.com/1996-1073/12/6/1074/htm
- Atlas Obscura. “Oxford Electric Bell.” https://www.atlasobscura.com/places/oxford-electric-bell
- Group14 Technologies, Inc. “The Transition to Lithium-Silicon Batteries.” Whitepaper. https://www.group14.technology/resources/whitepapers/whitepaper-the-transition-to-lithium-silicon-batteries/