Wolfspeed Grows to Meet Supply Challenge and Launches High Performance Gen 3+ Die
Article
Silicon Carbide (SiC), known for long as the ideal semiconductor technology for power devices, has with design and manufacturing innovation not only increased its share of the existing market but enabled new applications, such as electric vehicles (EVs), by offering higher power density, better high-speed switching performance, higher breakdown field, higher thermal conductivity, higher chip temperatures, and lower leakage currents than are possible with Silicon (Si).
Wolfspeed has led the SiC industry with the first commercial wafers in 1991, diodes in 2001, and MOSFETs in 2011. The company’s technology development has supported its relentless march toward larger wafer diameters and lower costs, higher quality, and greater device performance. The company has more than 35 years of SiC development experience and over 7 trillion device field hours.
This widely recognized success is evident from its recent selection by General Motors (GM) as their strategic SiC power device supplier [1]. GM is participating in the Wolfspeed Assurance of Supply Program (WS AoSP) for domestic, sustainable, and scalable materials in EV production.
It comes as no surprise that the same success was recently responsible for a rapid, wafer-shortfall-inducing growth in SiC demand from EV, solar and datacenter applications.
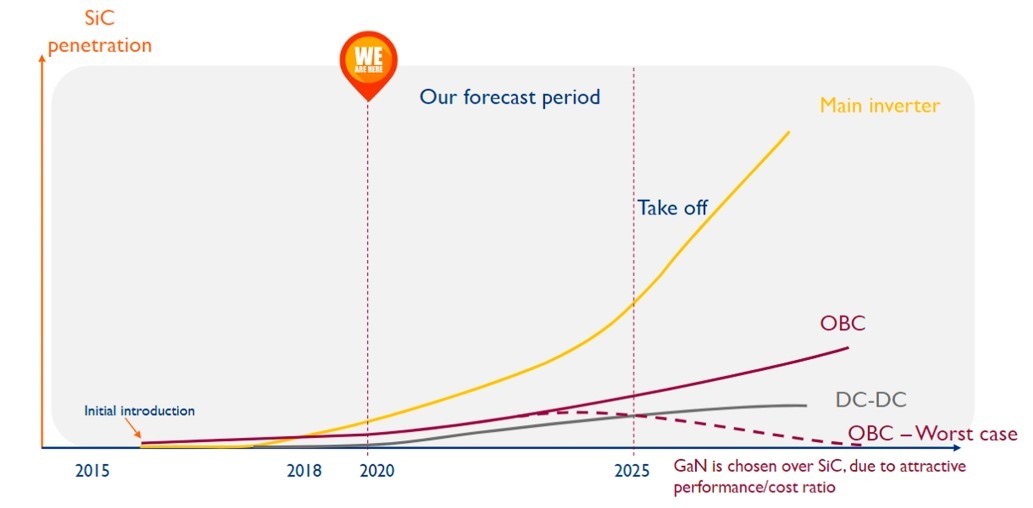
Yole Devéloppement forecasts the EV market the biggest opportunity for SiC, worth over $5 billion in 2027, while the charging infrastructure market continues growing at 90% CAGR through 2025. Yole expects SiC to gain market share in the long term as companies like Wolfspeed overcome all challenges, including those related to supply, cost, and performance (Figure 1).
Resolving supply & cost challenges
Commanding nearly 60% of the N-type SiC substrate market in 2018-2019 as estimated by Yole, Wolfspeed is naturally the supplier to resolve supply challenges due to growing market confidence in SiC. The company is investing $1 billion in a new 200-mm wafer-capable Mohawk Valley Fab (MVF) [2] and converting its existing facility into a materials mega-factory.
While competitors are still using 150-mm fabs, Wolfspeed is leveraging vertical integration and internal “cycles of learning” to address demand and cost with 200-mm wafers from the new automotive-qualified automated facility.
The MVF construction is complete, the first 200-mm wafers demonstrated, and the fab is undergoing qualification for mass production.
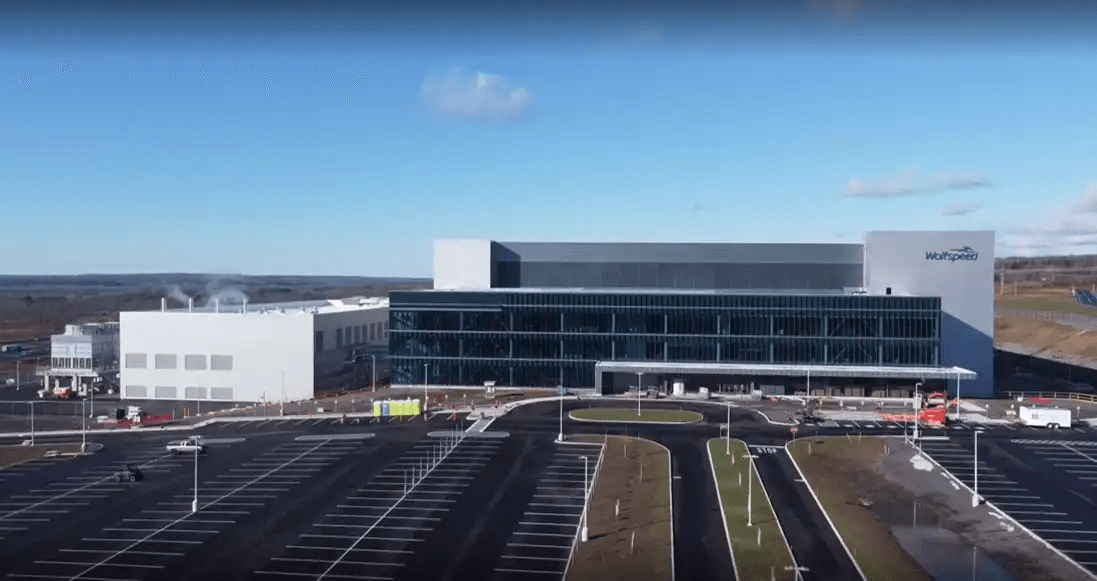
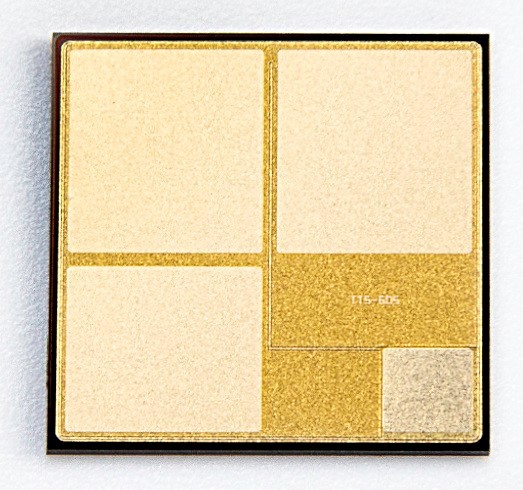
Upping the performance ante
Among key performance parameters that help meet EV requirements are the SiC MOSFET drain-to-source ON resistance, RDS(ON), and rated junction temperature, Tj, with the former responsible for conduction losses and thermal waste and the latter the device reliability and its ability to withstand heat.
Wolfspeed has continued innovation to address these concerns with a new Gen 3+ 750 V bare-die MOSFET (Figure 3) that has already won several contracts. Coming in a 5mm x 5mm-layout and 180-mm thickness, it features low internal gate resistance Rg to optimize current rise-time and switching losses. Importantly, the new device boasts low on-state resistance (RDS(ON)) and high maximum junction temperature (TJ).
Compared with Wolfspeed’s 650 V, 15 mΩ MOSFET die with Tj rated to 175°C, the Gen 3+ product improves on RDS(ON) per unit area as well as total area to reach 10 mΩ. The 750 V rating improves the FIT rate and the MOSFET also elevates the Tj rating to above 175°C (200°C data shown) for peak condition operation during the vehicle mission profile. The temperature-stable RDS(ON) increases overall efficiency as well as system temperature limits (Figure 4).
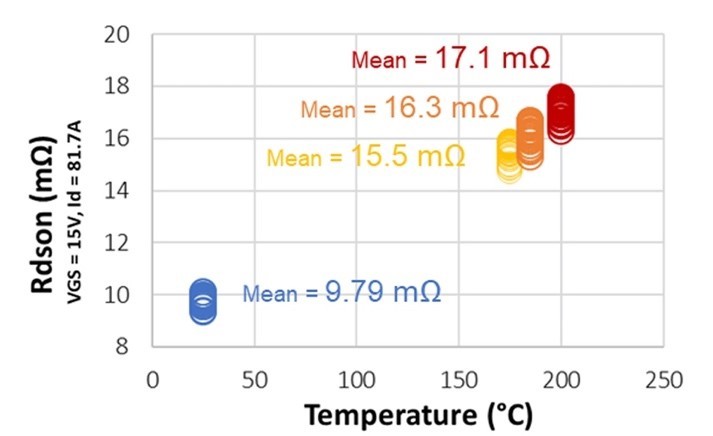
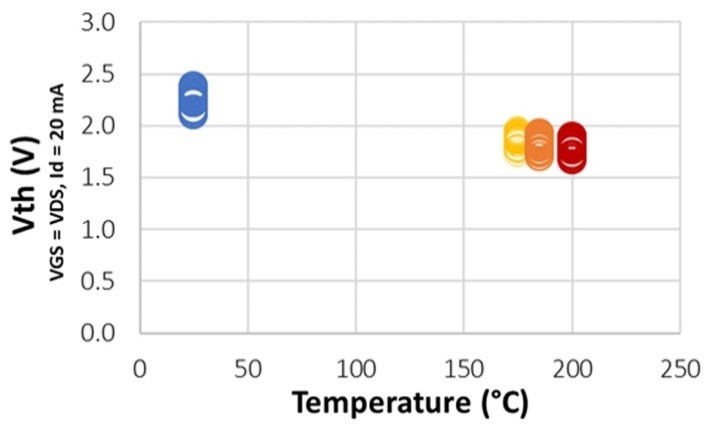
Gen 3+ technology offers similar stability for the gate threshold voltage, Vth, giving designers enough headroom to switch aggressively while avoiding spurious turn-on (Figure 5). Combined with a high capacitance ratio, the stable Vth allows for safe operation without shoot-through concerns at elevated temperatures.
Moreover, Wolfspeed uses an Ni/Pd/Au metallization stack-up on both die sides to allow double-sided soldering/sintering. This new metallization used on Wolfspeed’s automotive die opens the option for more advanced packaging solutions that can lead to better performance from the die and better reliability of the package. Examples of this include sintering copper clips or films to the top of the die and using copper wire bonds for higher current carrying and thermal capabilities (Figure 6).
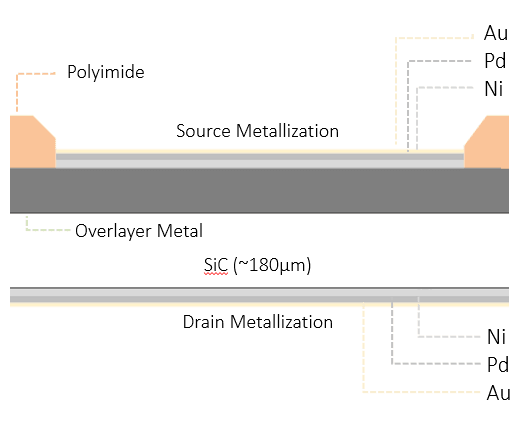
Robust performance for automotive apps
The AEC-Q101-qualified MOSFETs are robust enough to withstand failure modes like short circuit and surge, which are important factors to consider in automotive applications where high robustness is necessary.[3]
This die has high energy capabilities of 1.2 J in short circuit conditions and >2.6 ms withstand time at a junction temperature of 175°C. This short circuit withstand time (tested under worst case conditions) offers an adequate safety margin for gate driver technology to handle the fault. The devices have also been tested to withstand surge currents of up to 340 A or, depending on application conditions, >3x rated current. This surge current capability is important for active short circuit modes or other high current events.
The die is also capable of withstanding high temperature excursion events up to 200°C for a limited time without affecting device reliability. This functionality was demonstrated with extended high temperature AEC-Q101 tests at 200°C for 168 hours.
Switching performance tests under standard conditions demonstrated 30 V/ns and 4 A/ns switching speeds, without exceeding the voltage rating during transients. The device also exhibited consistent switching losses over temperature, with only a 150 µJ increase in total switching losses in a device tested from 25°C to 175°C. The fast switching capability of these devices and stable operation over temperature leads to overall lower switching losses in the system.
Summary
Wolfspeed has shared new details of its 200 mm expansion and new automotive-qualified 750 V Bare Die MOSFETs designed for use in electric vehicle powertrain applications. Robust operation to 200°C, strong short-circuit energy (1.2 J) and time (> 2.6 ms) capabilities, surge currents up to 340 A, and low (10 mΩ) conduction losses have enabled the 750 V, 10 mΩ SiC MOSFETs to be successfully designed into new battery electric vehicles.
References
- Cree Becomes Wolfspeed, GM Deal Signals The Coming End Of The ICE Age (forbes.com)
- Wolfspeed to Build New SiC Manufacturing Facility at Marcy Nanocenter | Regional Economic Development Councils (ny.gov)
- A. Romero, et al, “High Temperature Performance of Next Generation 1200V SiC MOSFET die with Advanced Packaging Technology,” PCIM, May 2022.